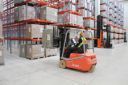
Per utilizzare questa funzionalità di condivisione sui social network è necessario accettare i cookie della categoria 'Marketing'
![]()
Questo articolo è pubblicato sotto una Licenza Creative Commons.Per visualizzare questo banner informativo è necessario accettare i cookie della categoria 'Marketing'
Storie di infortunio: l’ultimo giro di giostra
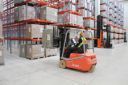
Grugliasco (TO), 17 Giu – Il Centro regionale di Documentazione per la Promozione della Salute della Regione Piemonte ( Dors) raccoglie storie d'infortunio rielaborate dagli operatori dei Servizi PreSAL delle ASL piemontesi a partire dalle inchieste di infortunio, con la convinzione che conoscere come e perché è accaduto sia una condizione indispensabile per proporre soluzioni efficaci per la prevenzione. In questa storia, dal titolo “L’ultimo giro di giostra” (a cura di Giampiero Bondonno, Savina Fariello Servizio Pre.S.A.L. della Asl BI), un lavoratore viene ritrovato esamine sulla sommità di un carro semovente automatico, schiacciato tra il carro e una trave in cemento armato della volta del magazzino.
Che cosa
Un manutentore che si occupa di installazione di impianti per magazzini automatizzati viene ritrovato esamine sulla sommità di un carro semovente automatico, schiacciato tra il carro e una trave in cemento armato della volta del magazzino. Il lavoratore stava svolgendo delle operazioni di manutenzione all’interno di un magazzino automatizzato in un’azienda tessile.
Chi
Giuseppe era un lavoratore italiano di 41 anni con esperienza pluriennale nel campo della manutenzione di magazzini automatizzati. Circa sei anni prima aveva lavorato all’installazione dello stesso magazzino come dipendente della ditta costruttrice. Nonostante la chiusura della ditta, aveva continuato a occuparsi della manutenzione dei magazzini automatizzati presenti sul territorio italiano per conto della ditta che era subentrata alla ditta costruttrice.
Pubblicità
Dove e quando
L’infortunio mortale è avvenuto in Piemonte nel febbraio 2008 all’interno di un capannone industriale di un’azienda tessile. In un locale seminterrato è installato un magazzino automatizzato denominato “impianto magazzinaggio e smistamento pezze”.
L’impianto è installato nel magazzino a pianta rettangolare, costituito da tre lunghi corridoi paralleli ove sono collocate le scaffalature per il deposito delle pezze di tessuto e da altri tre corridoi trasversali ai primi.
Esiste poi un quarto corridoio, parallelo ai primi tre e non interconnesso con gli altri, lungo il quale si muove un carrello a percorso fisso.
All’interno dell’impianto operano tre carri semoventi tipo AGV (Automatic Guided Vehicles) alimentati elettricamente da una batteria ricaricabile sistemata a bordo. Una centralina gestita dal software dell’impianto produce il segnale elettromagnetico che guida i tre carri tramite un conduttore annegato nel pavimento di cemento; in questo modo i tre carri AGV si possono muovere liberamente all’interno del magazzino.
Questi tre carri svolgono la funzione di “magazzinieri”, prelevando le pezze depositate nei contenitori di arrivo in magazzino mediante il carrello a percorso fisso, e provvedono a depositarle sugli scaffali del magazzino. Svolgono poi l’operazione contraria quando le pezze devono essere prelevate per la spedizione ai clienti.
È importante sottolineare che il personale dell’azienda tessile inserisce via terminale nel software dell’impianto le richieste sia di immagazzinaggio, sia di prelevamento delle pezze. Pertanto, il personale non può né determinare quale carro realizzerà materialmente l’ordine impartito, né vedere i movimenti dei carri.
Il responsabile del magazzino (un preposto dell’azienda tessile) aveva contattato la ditta per la quale Giuseppe lavorava perché si era verificato un malfunzionamento nelle operazioni di carico e scarico delle pezze. Uno dei tre carri semoventi automatici senza conducente installati all’interno del magazzino non funzionava poiché non riceveva il segnale a radiofrequenza utilizzato per la trasmissione dei dati operativi.
Come
Quella mattina Giuseppe è arrivato presso lo stabilimento tessile alle 6:30 (dall’analisi della scheda d’intervento che ha compilato) ed è andato subito nel magazzino per eseguire l’intervento di manutenzione richiesta. Gli altri lavoratori dell’azienda tessile hanno visto e incontrato Giuseppe, intento alle sue faccende, sia in magazzino che in altre zone dello stabilimento fin verso le dieci e mezza, dieci e quarantacinque. Dopo quell’ora nessuno l’ho ha più visto sino a quando il preposto dell’impianto lo ha trovato schiacciato tra una trave ribassata del soffitto e la parte superiore del carro semovente.
“Ero sceso per avvertire Giuseppe che il suo responsabile non riusciva a contattarlo al telefonino. Erano circa le 11:30 e ho notato il carro numero 1 fermo nel mezzo del magazzino. Appena mi sono avvicinato ho visto Giuseppe schiacciato tra il soffitto e il carro e ho chiamato i miei colleghi per tentare di liberarlo”.
Il corpo di Giuseppe era sulla sommità della cabina elettrica/elettronica del carro AGV identificato con il numero 1. Il carro si trovava in uno dei corridoi trasversali del magazzino, per la precisione il secondo partendo dalla zona di accesso al magazzino. Questi corridoi sono percorsi dai carri AGV per collegarsi con i corridoi più lunghi dove sono collocati gli scaffali di deposito delle pezze. Nello specifico il carro era fermo nello spazio tra due corridoi lunghi, come se stesse andando da uno di questi verso un altro.
Al momento del sopralluogo il carro numero 1 era fermo, in condizione di allarme, con il corpo di Giuseppe incastrato tra i montanti metallici della cabina e una trave ribassata in cemento armato, sporgente dal piano di soffitto del magazzino. La distanza tra la sommità della struttura del carro e la trave era di circa 20 cm.
Sotto il corpo di Giuseppe si intravedeva un’attrezzatura di lavoro e dei fili elettrici che andavano a una scheda elettronica del carro. Il riparo in lamiera del quadro elettronico di bordo macchina del carro non era inserito nella sua sede ma si trovava in una zona del magazzino, come se fosse stato tolto per poter lavorare sul quadro.
Dopo che i Vigili del Fuoco hanno liberato il corpo di Giuseppe, si è constatato che la strumentazione nascosta dal corpo era un oscilloscopio portatile di proprietà della ditta di manutenzione e usato da Giuseppe e che i cavi collegavano l’oscilloscopio a una scheda elettronica del carro.
Perché
Giuseppe aveva terminato le operazioni di manutenzione e dopo aver compilato la scheda d’intervento, si accingeva a lasciare il magazzino. Probabilmente si è accorto di aver dimenticato l’oscilloscopio portatile sulla parte superiore del carro AGV n. 1 e, per andare a riprenderlo, è entrato nell’area segregata e pericolosa dell’impianto con il magazzino funzionante in modalità automatica.
Giuseppe si è diretto verso il carro AGV n. 1 che era fermo in attesa di missioni nel primo corridoio nella zona di sinistra del magazzino ed è salito sulla parte posteriore del carro. Non ha utilizzato la scaletta in dotazione che avrebbe interrotto il funzionamento in automatico del carro, ma si è arrampicato appoggiando i piedi sulla cornice inferiore del quadro elettrico e aiutandosi con la scaffalatura posta alla sua sinistra. In quel momento il carro era fermo nella posizione A della planimetria allegata.
Poiché l’impianto funzionava in automatico è probabile che il carro AGV n. 1 abbia ricevuto una missione e si sia messo in movimento dirigendosi verso la prima rotatoria, identificata con B in planimetria, cogliendo di sorpresa l’infortunato e costringendolo ad aspettare il successivo arresto per scendere.
Secondo la ricostruzione effettuata esaminando i tracciati informatici, il carro si è diretto, verso la prima rotatoria con Giuseppe bloccato a un’altezza di circa 1,40 – 1,50 m dal suolo, ha effettuato una rotazione sul suo asse di 90° e si è immesso nel corridoio centrale, dirigendosi verso la seconda rotatoria. Dopo aver percorso pochi metri nel corridoio centrale, il carro doveva passare sotto una trave ribassata, con una distanza di circa 20 cm dal limite superiore di ingombro del carro AGV n. 1. Giuseppe, non potendo vedere in quanto di spalle rispetto al senso di marcia, ha urtato la trave con la schiena e, piegandosi in avanti, si è incuneato tra la sommità del carro e la trave, rimanendo schiacciato. A causa dello sforzo, il carro è slittato verso destra e ha perso il segnale della traccia annegata nel pavimento, fermandosi nella posizione C.
Il corpo di Giuseppe è rimasto incuneato e bloccato nella posizione D dove è morto.
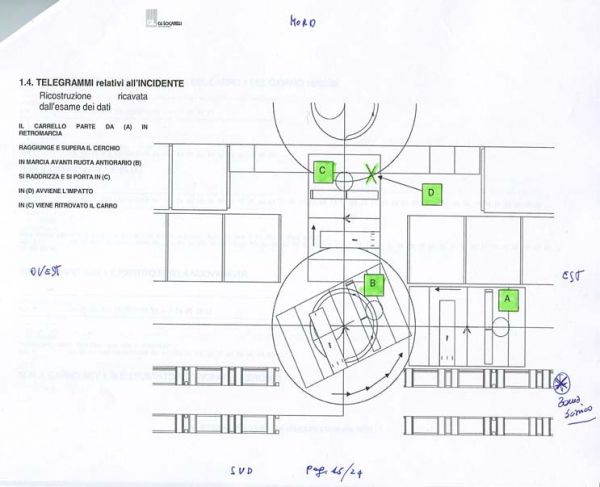
Cosa si è appreso dall’inchiesta
Giuseppe è potuto entrare nella zona pericolosa con i tre carri AGV operanti in modalità automatica, in quanto il magazzino era completamente difforme, per quanto riguarda la sicurezza degli operatori, a quanto specificato nel manuale d’uso e manutenzione.
Infatti, esistevano molte elusioni e bypass delle sicurezze che permettevano l’ingresso, la sosta e il transito in tutte le aree definite pericolose (e quindi obbligatoriamente da proteggere e segregare) dal manuale d’uso e manutenzione dell’impianto.
La verifica dell’impianto ha permesso di evidenziare diverse mancanze, elusioni e violazioni delle norme di sicurezza e, in particolare:
· l’unica fotocellula posta a protezione dell’ingresso pedonale della zona magazzino era danneggiata e non funzionava. Si poteva quindi entrare in qualsiasi momento nella zona pericolosa del magazzino, senza che i carri AGV interrompessero il movimento in automatico. Per non interrompere il funzionamento del magazzino la fotocellula danneggiata era inoltre elusa come specificato di seguito;
· la centralina di sicurezza posta nel quadro principale dell’impianto era manomessa mediante un collegamento, in gergo “cavallottamento”, realizzato con due fili elettrici. In questo modo l’impianto di magazzinaggio funzionava in qualsiasi modalità operativa (automatico e manuale) ed era inibita la protezione perimetrale rappresentata dalla fotocellula danneggiata indicata sopra. L’elusione della fotocellula, permetteva l’accesso dei lavoratori all’interno dell’area con i carri in movimento con il conseguente rischio di investimento. Era così preclusa l’attuazione delle procedure di sicurezza, previste nel manuale d’uso e manutenzione dell’impianto, relative all’ingresso sicuro (a carri fermi) all’interno dell’area pericolosa;
· nel magazzino erano stati installati due quadri elettrici per l’alimentazione e la gestione operativa dell’impianto. Il quadro principale, nella zona d’ingresso del magazzino, serviva per accendere e spegnere l’impianto, consentendo l’accesso in sicurezza nelle aree pericolose. Il secondo quadro, derivazione del principale, si trovava all’interno dell’area pericolosa del magazzino. Dalle indagini svolte si è accertato che il quadro principale non era utilizzato e tutta la gestione del magazzino era effettuata impiegando il quadro secondario. I lavoratori non avevano alcuna possibilità di operare in condizioni di sicurezza in quanto i collegamenti tra i due quadri elettrici erano elusi o mancanti e quindi tutte le sicurezze che, secondo il progetto dell’impianto, dovevano essere gestite dal quadro principale non erano utilizzabili. In questo modo l’intero magazzino era privo di qualsiasi tutela nei confronti dei lavoratori, consentendo l’accesso nelle zone pericolose con l’impianto funzionante.
È verosimile che l’impianto abbia funzionato senza le sicurezze previste dal costruttore fin dalla sua installazione. Infatti, le manomissioni e le esclusioni effettuate sull’impianto erano complesse e probabilmente sono state realizzate da persone specializzate e non dai manutentori dell’azienda utilizzatrice.
La pericolosità dell’impianto è stata sottovalutata ignorando le possibili casistiche d’infortunio. È probabile che la ditta utilizzatrice abbia valutato solamente le attività attuate dai propri dipendenti all’interno del magazzino trascurando gli interventi di manutenzione che si sarebbero svolti. A sostegno di questa tesi si evidenzia che erano stati installati sui carri AGV dei dispositivi supplementari di sicurezza a “costa sensibile”, in grado cioè di bloccare immediatamente il carro in movimento, se urtati dal lavoratore in transito. Dispositivi che, se l’impianto fosse stato installato secondo progetto, erano ridondati con le sicurezze perimetrali ma nel caso specifico rappresentavano l’unica sicurezza, contro il rischio di investimento per i lavoratori del magazzino. Non sono stati considerati i rischi per i manutentori dell’impianto, (ad esempio cesoiamento, schiacciamento, ecc…) nel caso di accesso all’area pericolosa del magazzino.
Infine, nelle procedure di manutenzione, non erano state considerate le relazioni tra i diversi operatori dell’impianto e le relative responsabilità. In particolare, si è lasciato Giuseppe in solitudine all’interno del magazzino non preoccupandosi di interrompere il ciclo lavorativo, ossia le richieste inviate dal personale della ditta tessile al software dell’impianto, creando involontariamente la situazione di pericolo che ha causato l’infortunio
Indicazioni per la prevenzione
Se si fossero rispettate pienamente le misure di prevenzione progettate dal costruttore, l’impianto sarebbe risultato sicuro per i lavoratori.
La valutazione del rischio da parte dall’azienda che installa un impianto nel proprio stabilimento, deve prendere in considerazione i rischi sia per i propri dipendenti sia per chi si occupa della manutenzione dell’attrezzatura.
Le indicazioni per la prevenzione emerse da questo infortunio raccomandano di valutare l’impianto considerando il suo effettivo utilizzo in azienda e i rischi a esso correlati. In particolare, occorre tenere in considerazione gli usi previsti e imprevisti, nonché le attività di manutenzione necessarie per il mantenimento dell’impianto in condizioni di sicurezza.
È necessario, inoltre, stilare una procedura per gestire le operazioni di manutenzione che preveda che nessuno possa intervenire da solo sull’impianto e che l’impianto, durante il permanere delle persone nell’area pericolosa, sia completamente non operativo.
Come è andata a finire
“A distanza di alcuni mesi, sono andato a verificare se le sicurezze progettuali dell’impianto fossero ancora funzionanti come avevamo prescritto. Il magazzino era in uso
e le sicurezze idonee ed utilizzate. Bastava veramente poco per impedire una tragedia…”.
Fonte: Dors.

Pubblica un commento
Rispondi Autore: Mario Maiolani ![]() | 17/06/2014 (11:30:51) |
C'è poco da commentare: è condizione usuale che i manutentori, perfetti conoscitori degli impianti, spesso si fidano troppo della loro esperienza. Questosuccede comunque in ogni attività lavorativa e nella conduzione dei veicoli: sono i lavori di routine o i minimi interventi occasionali che "fregano". |
Rispondi Autore: giampiero bondonno ![]() | 23/06/2014 (13:54:23) |
mi pare riduttivo pensare che "è condizione usuale che i manutentori, perfetti conoscitori degli impianti, spesso si fidano troppo della loro esperienza". nel caso in esame l'impianto era non sicuro per chiunque e non solamente per il manutentore della ditta esterna. In anni di attività ben poche volte ho ritrovato, nello stesso impianto, le elusioni e il mancato rispetto della normativa antinfortunistica che esistevano, in quel magazzino, al momento dell'infortunio. pensare che un infortunio del genere, nella sua gravità, sia imputabile solamente al comportamento del lavoratore è estremamente sbagliato e non corrisponde al vero. |