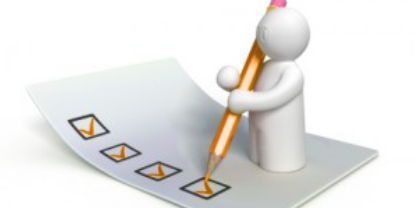
Per utilizzare questa funzionalità di condivisione sui social network è necessario accettare i cookie della categoria 'Marketing'
Questo articolo è pubblicato sotto una Licenza Creative Commons.Per visualizzare questo banner informativo è necessario accettare i cookie della categoria 'Marketing'
Sicurezza delle macchine: una check list per l’autovalutazione
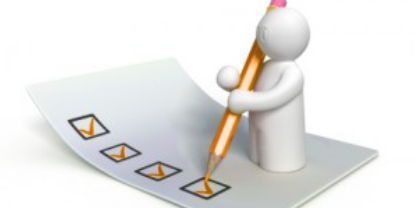
Treviso, 4 Lug – In questi mesi ci siamo soffermati, con riferimento anche a quanto indicato dal D.L. n.5 del 9 febbraio 2012 in merito alla disciplina dei controlli sulle imprese, su alcune azioni volte a favorire la trasparenza dell'attività di controllo e a migliorare l'ottemperanza, da parte delle aziende, alle misure di prevenzione in materia di tutela di salute e sicurezza.
Ad esempio abbiamo presentato – come pubblicati nello spazio web dell’ Azienda ULSS 9 di Treviso - materiali e check list che permettono non solo di conoscere le modalità con cui lo SPISAL effettua i controlli durante la vigilanza negli ambienti di lavoro, ma anche di conoscere le norme da rispettare e di autovalutare nelle aziende il grado di conformità alla normativa sulla sicurezza.
Pubblicità
Ci soffermiamo oggi in particolare sulla “Scheda valutazione: Protezione delle attrezzature di lavoro dai rischi meccanici”, aggiornata nel mese di aprile 2016. Una check list che è stata prevista per l'autovalutazione da parte delle aziende, in materia di sicurezza delle macchine.
La check list è stata elaborata con riferimento alle “problematiche più frequenti e alle modalità con cui viene usualmente effettuato il controllo in azienda da parte dello SPISAL”.
È evidente, sottolinea la presentazione dell’ULSS 9 della check list, che al di là di quanto riportato non si esclude “l'obbligo di rispettare comunque tutte le indicazioni previste dalla normativa”.
La scheda di autovalutazione è divisa in varie sezioni. Per ogni sezione sono proposte diverse domande per verificare la conformità alla normativa e nella parte con le “istruzioni per la compilazione” sono riportate ulteriori indicazioni, per ogni domanda, sui riferimenti normativi, sulle istruzioni per l’azienda e su annotazioni specifiche.
A titolo esemplificativo riportiamo le domande della sezione 1 - Corretta installazione e uso secondo le previsioni del fabbricante:
- “le attrezzature sono installate come previsto dal costruttore (CE) o dall’allegato V – VI DLgs 81/08 (non CE)?
- le attrezzature la cui sicurezza dipende dalla corretta installazione, sono state sottoposte a controllo iniziale dopo il montaggio (attestazione di corretta installazione)?
- le attrezzature sono impiegate per l’uso/tipo di lavorazione previsto dal costruttore?
- le attrezzature sono impiegate correttamente dai lavoratori?
- le attrezzature marcate CE dispongono di istruzioni per l’uso”?
E nelle istruzioni si indica che “per le macchine marcate CE, il costruttore deve indicare come installare la macchina (incluse eventuali istruzioni per il montaggio); inoltre devono essere rispettate le indicazioni dell’allegato VI. Per le macchine non marcate CE l’installazione deve rispettare le indicazioni degli allegati V e VI del DLgs 81/08”.
Inoltre il controllo dopo l'installazione prima della messa in esercizio “deve essere eseguito da persona competente; la responsabilità della scelta ricade sul Datore di lavoro. A seguito del controllo è opportuno sia rilasciato un documento che attesti la corretta installazione”.
Riguardo poi all’impiego corretto, si segnala che il lavoratore ha “l’obbligo di utilizzare correttamente l’attrezzatura ma il preposto, il dirigente e il datore di lavoro hanno l’obbligo di vigilare sul rispetto di tale indicazione. Le attrezzature potranno essere utilizzate solo da lavoratori appositamente incaricati e formati/addestrati/abilitati”.
Ci soffermiamo brevemente anche sulla sezione 3 - Controlli e manutenzione, con riferimento alla domanda:
- la manutenzione “comprende anche il mantenimento dei requisiti di sicurezza”?
Nelle istruzioni si indica che non solo le manutenzioni “dovranno essere finalizzate anche al mantenimento dei requisiti di sicurezza”, ma che le misure di prevenzione “dovranno essere aggiornate in relazione ai mutamenti organizzativi e produttivi che hanno rilevanza ai fini della salute e sicurezza del lavoro, o in relazione al grado di evoluzione della tecnica della prevenzione e della protezione”. E “oltre al funzionamento dell’attrezzatura a fini produttivi, deve essere verificata sistematicamente anche l’efficienza deisistemi di protezione”.
La sezione 4 è dedicata proprio ai sistemi di protezione e ai ripari, anche con riferimento alla norma UNI EN ISO 13855.
I ripari “devono essere di costruzione robusta, fissati solidamente e difficilmente eludibili. La loro distanza dalla zona pericolosa dovrà essere adeguata al rischio. È importante che non siano d'intralcio né all'osservazione del ciclo di lavoro, né tantomeno all'esecuzione del lavoro stesso, onde evitare la tentazione di eluderli”. Inoltre le distanze di sicurezza “devono essere misurate a partire dalla superficie che limita il movimento del corpo o della sua parte più sporgente, tenendo conto che il lavoratore potrebbe sforzarsi a protendere parti del corpo oltre la struttura di protezione, con l'intenzione di raggiungere la zona pericolosa. Non si devono utilizzare mezzi, quali scale o sedie, per cambiare il piano di riferimento, né sbarre o utensili per aumentare l'accessibilità naturale degli arti superiori. La posizione del dispositivo deve essere progettata tenendo conto della velocità di avvicinamento e del tempo di arresto dell’elemento mobile pericoloso”. E i ripari possono essere di diverso tipo (fisso, regolabile, mobile interbloccato, barriere optoelettroniche, laser scanner, tappeti sensibili, ...) e “devono essere del tipo idoneo a funzioni di sicurezza (EN 61496)”.
Rimandando ad una lettura integrale della check list, che si sofferma in specifico sui ripari fissi, sui ripari mobili interbloccati e sui ripari regolabili, fermiamo la nostra attenzione sulla parte relativa alla segregazione della aree pericolose (Sezione 4d):
- “nel caso di protezioni perimetrali di aree pericolose, sono assenti varchi non protetti che consentono l’accesso delle persone?
- se sono presenti porte o cancelli di accesso all’interno dell’area protetta, questi sono dotati di interblocco” (con i requisiti previsti nella precedente sezione 4b)?
Nelle istruzioni si indica che “qualora fosse possibile delimitare una zona in cui relegare attrezzature che, singolarmente o globalmente, possano costituire rischio per la salute o sicurezza, tutta l’area dovrà essere resa inaccessibile alle persone durante il funzionamento anche di una sola macchina”. E in particolare le aperture che si trovano nella parte bassa delle recinzioni perimetrali “devono avere dimensioni tali da impedire di raggiungere parti pericolose in funzione della distanza di sicurezza e della parte del corpo (arti inferiori). Non deve essere consentito il passaggio del corpo intero”.
Inoltre è indispensabile che “tutti gli accessi protetti da porte o cancelli dotati di interblocco, con la loro apertura siano in grado di interrompere il moto di tutte le macchine costituenti pericolo presenti all’interno dell’area”.
È presente, infine, una sezione dedicata ai “particolari aspetti connessi alle attrezzature per il sollevamento e la movimentazione merci (accessori di sollevamento, percorsi)”.
Riguardo ai percorsi si indica che “ove possibile è opportuno tenere separati con apposita segnaletica orizzontale i percorsi dei mezzi e dei pedoni. Le aree promiscue devono essere chiaramente indicate. Davanti alle uscite che immettono direttamente sulle vie di transito dei mezzi, se possibile devono essere poste barriere atte ad evitare investimenti”.
inoltre è opportuno “definire, anche con procedure scritte e comunicate ai lavoratori, le regole per transitare (inclusa la precedenza) negli spazi rispettivamente destinati al solo transito dei mezzi, ai soli pedoni e all’uso misto. Particolare attenzione deve essere posta a soggetti esterni che entrano in azienda (es. trasportatori)”.
Concludiamo riportando l’indice della check list:
- Sezione 1 – Corretta installazione e uso secondo le previsioni del fabbricante
- Sezione 2 – Omologazioni – Prima verifica - Verifiche periodiche
- Sezione 3 – Controlli e manutenzione
- Sezione 4 – Ripari
- Sezione 4a - Ripari fissi
- Sezione 4b - Ripari mobili interbloccati
- Sezione 4c - Ripari regolabili
- Sezione 4d - Segregazione aree pericolose
- Sezione 5 – Dispositivi di comando, arresto di emergenza
- Sezione 6 – Procedure per registrazione, anomalie, manutenzione, etc.
- Sezione 7 – Formazione - addestramento dei lavoratori – abilitazioni
- Sezione 8 – Particolari aspetti connessi alle attrezzature per il sollevamento e la movimentazione merci (accessori di sollevamento, percorsi).
ULSS 9 Treviso, ULSS 8 Veneto, ULSS 7 Veneto, “ Scheda valutazione: Protezione delle attrezzature di lavoro dai rischi meccanici”, documento elaborato dal Dipartimento di Prevenzione U.O.C. SPISAL - Servizio Prevenzione Igiene e Sicurezza in Ambienti di Lavoro, versione V1.4 del 22 aprile 2016 (formato PDF, 375 kB).
Tiziano Menduto
