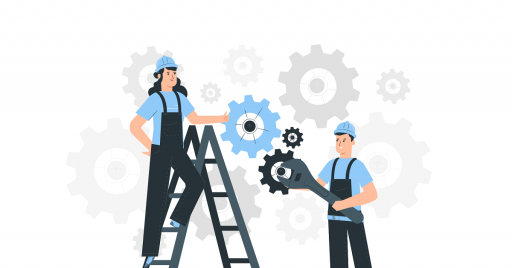
Per utilizzare questa funzionalità di condivisione sui social network è necessario accettare i cookie della categoria 'Marketing'.
Simulazione dinamica del processo di manutenzione basato sul rischio
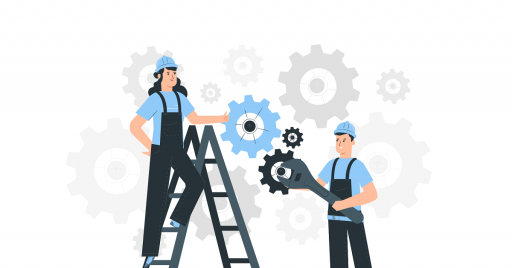
Pubblichiamo un estratto della relazione “Simulazione dinamica del processo di manutenzione basato sul rischio” presentata in occasione della VI edizione Safapche evidenzia come la pianificazione della manutenzione possa contribuire significativamente alla minimizzazione del rischio e diventare un’attività strategica nella gestione del rischio di un’organizzazione.
Simulazione dinamica del processo di manutenzione basato sul rischio
L. C. Santillo, M. Gallo, M. Di Nardo, L. Monica, M. Madonna, F. Giacobbe
Negli ultimi anni si è passati dalla metodologia Reliability Centered Maintenance (RCM) alla Risk Based Maintenance (RBM) che prende in considerazione non solo gli aspetti economici e di affidabilità, ma anche la sicurezza del personale e l'impatto ambientale attraverso il ricorso a metodi di analisi del rischio. La RBM ha reso possibile l’integrazione del meccanismo di priorità degli interventi di ispezione nella pianificazione della manutenzione, focalizzando l’attenzione sui componenti che necessitano realmente delle azioni manutentive. Il primo vantaggio è sicuramente un decremento di tutti i costi legati alla gestione della manutenzione, dal costo del personale a quello di indisponibilità dei macchinari. Il secondo, di gran lunga più importante del primo, è legato all’aspetto della sicurezza: quest’ultima non è affatto intaccata dalla riduzione del numero di ispezioni, anzi, credere di poter ispezionare tutti i componenti con lo stesso grado di priorità non avrebbe consentito la previsione della totalità dei guasti su una linea di produzione.
Il presente lavoro presenta una procedura per la pianificazione degli interventi di manutenzione ed ispezione sulla base della metodologia innovativa definita Risk-based Inspection and Maintenance (RBIM). In particolare, il valore aggiunto del lavoro consiste nel correlare gli aspetti ispettivi e manutentivi alle caratteristiche produttive di un impianto industriale. Partendo dalle caratteristiche della metodologia di manutenzione/ispezione basata sul rischio, proposta in ambito europeo nel progetto denominato RIMAP (Risk-Based Inspection and Maintenance Procedures for European Industry) al fine di armonizzare le disposizioni nazionali di regolamentazione dell'UE relative ai programmi di ispezione e manutenzione, si è cercato di strutturare un modello di gestione che integrasse la produzione e la manutenzione basata sul rischio. Per raggiungere questo obiettivo è risultato indispensabile, ai fini della semplificazione della trattazione, partire dalle peculiarità sia del processo produttivo che manutentivo mettendo in rilievo le relazioni e le interdipendenze esistenti tra tutti i fattori che influenzano i fenomeni dinamici.
Metodologia per l’ottimizzazione della manutenzione e delle ispezioni: Risk Based Inspection and Maintenance (RBIM)
Partendo dal documento proposto dal CEN riguardante la metodologia RBIM nell'ambito del progetto RIMAP (Risk-Based Inspection and Maintenance Procedures for European Industry), che fornisce linee guida per lo sviluppo di un programma di manutenzione/ispezione basato sul rischio applicabile a diverse tipologie di industrie e a differenti attrezzature, il presente lavoro si propone di valutare l’impatto che una metodologia risk based per lo sviluppo del piano manutentivo/ispettivo ha sulla produttività del sistema. La procedura proposta si articola in cinque macro fasi (Figura 1):
1.Equipment analysis,
2.Risk analysis,
3.Survival data collection and analysis,
4.RBM decision making process,
5.Execution, reporting and performance review.
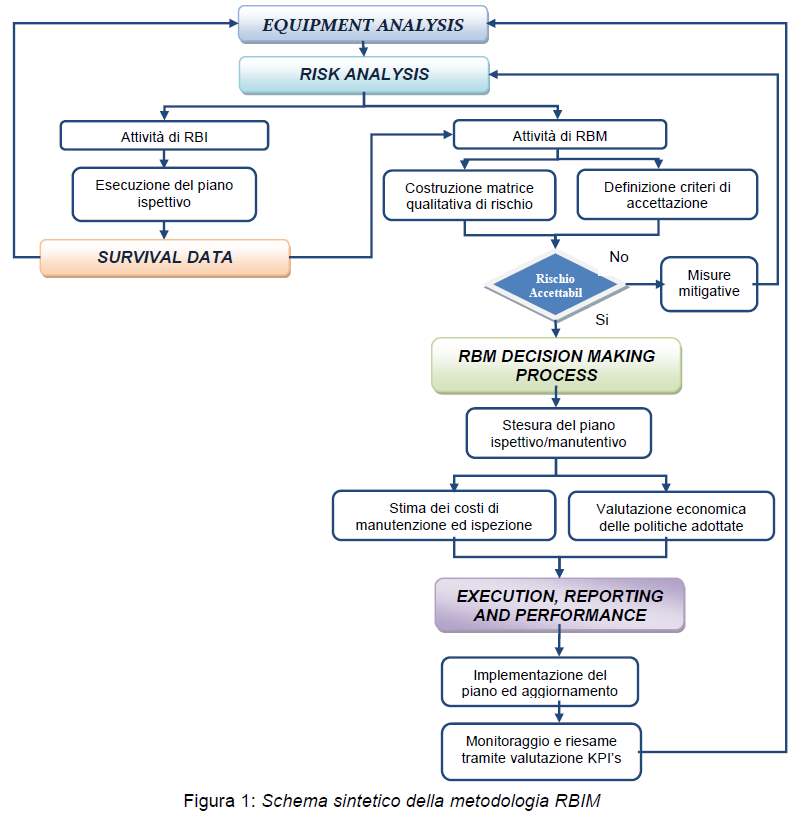
Equipment analysis
Il primo passo fondamentale del metodo è la raccolta di tutti i dati tecnici (P&ID, diagrammi logici, lista dei componenti, manuali, ecc.) necessari per l’analisi successiva, anche attraverso interviste al personale e consultazione degli archivi storici delle avarie e degli interventi di manutenzione/ispezione.
La metodologia parte quindi, in un approccio top-down, dall’individuazione dei livelli funzionali più importati dell’impianto e scende poi al livello di componenti o elementi strutturali da individuare come oggetto della manutenzione/ispezione. Il livello di dettaglio a cui la metodologia permette di arrivare dipende solo dalla presenza di dati affidabilistici sufficientemente dettagliati ed il più possibile personalizzati per l’impianto in analisi.
I sistemi sono generalmente definiti sulla base delle funzioni svolte e possono essere suddivisi in sottosistemi, al fine di creare una gerarchia funzionale che consenta di affrontare con maggiore facilità le criticità ad essi legate, quali ad esempio l’individuazione dei meccanismi di degrado dei componenti oppure la distribuzione della vita residua. Per stabilire il rapporto gerarchico, ogni sottosistema viene suddiviso in componenti che presentano delle interdipendenze di tipo strutturale, funzionale o stocastico.
L’individuazione dei componenti critici, invece, può essere realizzata con l’ausilio di norme specifiche per il campo di interesse (come ad esempio gli standard internazionali API 580/581 per le raffinerie petrolifere, o ancora la normativa Seveso III per la sicurezza degli impianti industriali); oppure con l’ausilio di strumenti largamente diffusi quali l’analisi FMECA e di Pareto, per quantificare l’impatto del guasto di un componente sulla produttività, sulla sicurezza e sull’ambiente. Per i sistemi e sottosistemi in osservazione, l’obiettivo dell’analisi è determinare le condizioni operative dei componenti e le situazioni eccezionali che potrebbero comportare guasti o malfunzionamenti del sistema. A tale scopo, risulta fondamentale identificare le fonti di informazione disponibili che possano fornire dati inerenti alla progettazione, al funzionamento ed alle ispezioni/manutenzioni. Prima di raccogliere le informazioni necessarie, sarebbe opportuno stimare la qualità e la quantità di dati necessari per effettuare una valutazione consistente della probabilità e delle conseguenze di uno scenario di guasto. I dati possono provenire da differenti aree: Produzione, Manutenzione e Servizio di Prevenzione e Protezione. I dati raccolti devono poi essere validati e successivamente immagazzinati
in database. Il processo di validazione prevede che le informazioni afferenti ad una stessa categoria vengano confrontate, controllandone la compatibilità con limiti fisici e tecnici mediante l’ausilio di standard o di linee guida. Il risultato di tale processo sarà una valutazione complessiva di tutti i dati rilevanti per la quantificazione del rischio dei componenti di interesse; definiti “raw technical data”.
Risk Analysis
Nella seconda fase della metodologia vengono definiti i parametri fondamentali per la valutazione del rischio, discriminando un’analisi preliminare da una dettagliata.
L’analisi preliminare dei componenti viene svolta in maniera rapida, semplice ed economica, esaminando una popolazione limitata di items. Da questa analisi, generalmente i sistemi e le apparecchiature vengono suddivisi in due gruppi: gli items ad alto rischio e gli items a medio/basso rischio. Soltanto per i primi verrà effettuata l’analisi dettagliata; mentre per i componenti caratterizzati da basso rischio sarà richiesta la minima sorveglianza, al fine di verificare ed assicurare che le assunzioni fatte in fase preliminare risultino ancora valide. Invece, per i componenti a medio rischio è necessario considerare ulteriori caratteristiche che consentano di decidere se eseguire la fase di analisi dettagliata o semplicemente un minimo controllo. Di solito, il livello iniziale di analisi è spesso sufficiente per evidenziare le aree dell’impianto con la più alta probabilità di guasto, eliminando dalle analisi successive le zone a basso e medio rischio. Il risultato ottenuto sarà costituito dai seguenti parametri:
- valore o categoria di probabilità di guasto (PoF) per la parte dell’apparecchiatura esaminata;
- valore o categoria di conseguenze di guasto (CoF) per la parte dell’apparecchiatura esaminata;
- valore o categoria di rischio per la parte dell’apparecchiatura esaminata dalla matrice di rischio preliminare.
L’analisi dettagliata, invece, si differenzia dalla precedente in termini di profondità richiesta per la valutazione del rischio. Infatti, per ogni sistema o gruppo di componenti ad alto rischio, viene identificato il meccanismo di degrado e viene stimata l’estensione del danno.
Sulla base di queste informazioni possono essere determinati gli intervalli per le attività di ispezione e manutenzione, in accordo con l’esigenza che il livello di rischio sia ancora accettabile. Tale analisi si articola in cinque compiti fondamentali:
A. identificazione dei pericoli;
B. identificazione dei meccanismi di degrado rilevanti e dei modi di guasto;
C. determinazione delle probabilità di guasto;
D. determinazione delle conseguenze di guasto;
E. valutazione del rischio.
Per l’individuazione dei pericoli, possono essere utilizzati diversi metodi quali: HAZOP; What-If Analysis e FMECA. Il compito di identificare i meccanismi di degrado rilevanti ed i modi di guasto risulta invece più complesso, in quanto è necessaria la conoscenza della funzione di guasto per poter listare tutti i possibili stati del componente durante i quali esso non svolge correttamente la performance richiesta. Inoltre dovrebbero essere inclusi non solo tutti gli eventi connessi ad uno specifico modo di guasto ma anche il tasso di deterioramento dell’attrezzatura. Generalmente, lo strumento utilizzato per risolvere tale problema è la Root Cause Failure Analysis (RCFA), che consente l’approfondimento dei meccanismi di degrado rilevanti.
Una volta determinati i meccanismi di degrado per i componenti critici, è possibile determinare le probabilità di guasto necessarie per la scelta delle strategie manutentive da implementare. La procedura RIMAP prevede l’utilizzo di tre differenti sorgenti di informazioni:
i. analisi statistiche dei dati storici;
ii. modellazione e previsione dei modi di guasto dei componenti;
iii. giudizio degli esperti.
Pertanto, la migliore stima della probabilità di guasto di un componente è fornita dalla combinazione di questi tre elementi.
Terminato il calcolo delle probabilità di guasto, si passa alla determinazione delle conseguenze di malfunzionamento considerando gli aspetti della salute, della sicurezza e della produzione. La quantificazione delle CoF per gli aspetti sopramenzionati richiede calcoli di diversi parametri quali: le proprietà dei materiali, la presenza di persone nell’area a rischio etc. Ai fini dell’elaborato è opportuno soltanto evidenziare che i riferimenti metodologici per l’effettuazione di questa fase sono riportati nel dettaglio nella procedura RIMAP. Infine, calcolate le PoF e le CoF, è possibile valutare il rischio ed inserire i risultati nella relativa matrice.
In questa macro fase si è determinato il rischio per ciascun componente critico, sulla base delle informazioni dei componenti ad alto rischio e dei dati relativi ai meccanismi di degrado; attraverso i quali è possibile determinare gli intervalli di ispezione e manutenzione teorici.
A questo punto si innesta la fase di Risk-Based Inspection, ricordando che l’attività di ispezione consiste nella “verifica della conformità mediante misurazione, osservazione, prova o rilevazione dimensionale delle caratteristiche relative ad un’entità”. Dunque le attività ispettive consistono principalmente nella stima dell’integrità strutturale delle attrezzature, mediante esami visivi o tecniche di controllo non distruttive, a supporto sia delle revisioni periodiche a cui i componenti pericolosi devono essere sottoposti, sia dell’adempimento alle verifiche di legge previste. In quest’ottica, le ispezioni rappresentano un sostegno per le attività manutentive in quanto consentono di valutare se l’attrezzatura è in grado di eseguire la funzione richiesta, mediante la misurazione del suo stato prestazionale. Con l’ausilio delle ispezioni si valutano quindi in maniera effettiva le condizioni dei componenti critici, correggendo le stime effettuate a priori senza la conoscenza del reale stato del componente, con le nuove informazioni raccolte nella fase RBI.
Survival data collection and analysis
I risultati derivanti dalla metodologia RBI consentono di stimare la probabilità di rottura di un’apparecchiatura, in funzione della distribuzione della vita media residua e dei possibili meccanismi di degrado; mentre le conseguenze di un guasto possono essere correlate alle condizioni operative in cui l’attrezzatura opera. Nella pratica, i nuovi dati resi disponibili mediante le ispezioni, consentono di effettuare una rivalutazione della vita residua di un componente e di conseguenza di migliorare la stima dell’affidabilità dello stesso. I principali approcci utilizzati per valutare l’affidabilità sulla base dei dati collezionati sono generalmente due: il primo approccio deriva direttamente dalle funzioni empiriche di sopravvivenza riguardanti il tempo al guasto del dispositivo e vengono definite funzioni empiriche correlate ai dati (Empirical Function Direct to Data). Il secondo approccio, chiamato di Ricerca di Distribuzioni Teoriche (Theoretical Distribution Research), è il più complesso ma anche il più appropriato in quanto considera distribuzioni quali: Weibull, Esponenziale, Normale etc. Tale approccio è preferibile poiché fornisce maggiori informazioni e soprattutto una valutazione migliore dell’affidabilità dei componenti. È opportuno osservare però che si potrebbe iniziare l’analisi con la procedura EFDD e successivamente considerare la TDR. Sulla base delle nuove informazioni legate alla distribuzione della vita media residua e all’affidabilità, è possibile effettuare una rivalutazione del rischio, necessaria per le attività di RBM, attraverso le quali si definisce la programmazione degli interventi manutentivi. La schedulazione dei suddetti interventi si fonda sul concetto di stabilire una priorità in base al livello di rischio dei componenti, analogamente a quanto fatto per le ispezioni; con l’unica differenza che per la determinazione del livello di rischio viene calcolata una matrice di tipo qualitativo, in cui le valutazioni si basano essenzialmente sull’esperienza ed sul know-how di esperti del settore.
Controllare il livello di rischio consente di variare le politiche manutentive a seconda dello stato dei componenti più critici, avendo ben chiaro quali sono le probabilità di accadimento di ogni singolo modo di guasto di ogni singolo componente, sempre correlato con le relative conseguenze economiche e di sicurezza.
La gestione delle priorità diventa, dunque, una fase preliminare alla preparazione ed alla pianificazione dei lavori di manutenzione ed è frutto di una valutazione collegiale di un gruppo di lavoro multidisciplinare, costituito da esperti del reparto produzione, ispezione, manutenzione e sicurezza. In base agli accordi tra le diverse funzioni coinvolte nella definizione delle priorità, vengono stabilite sia le date entro cui gli interventi manutentivi devono essere completati, che i criteri di accettazione dei livelli di rischio, sulla base delle norme vigenti. Quindi, il rischio di ciascun componente viene confrontato con il rispettivo livello di accettazione e se qualora non fosse accettabile si impostano specifiche misure mitigative.
Qualora il livello di rischio risultasse accettabile, si passerebbe alla fase successiva.
RBM Decision making process
Nel momento in cui il rischio risulta accettabile, è possibile implementare la quarta fase della metodologia, in cui viene proposto un piano di manutenzione che tenga conto, in prima istanza, dell’aspetto legato alla sicurezza ed all’ambiente, e che successivamente consideri l’aspetto economico; attraverso la stima dei costi relativi alle azioni manutentive da intraprendere ed alle politiche scelte. Sicuramente, nell’ambito del processo decisionale, il fattore economico assume un ruolo rilevante; per tale motivo, per ciascun componente critico analizzato, gli ingegneri della manutenzione, in collaborazione con lo staff di contabilità, reperiscono le informazioni legate ai costi degli interventi manutentivi, che ovviamente variano a seconda della politica adottata.
Se si volessero perseguire concomitantemente tutti i suddetti obiettivi, i costi legati al processo di manutenzione risulterebbero elevatissimi. Per questo motivo, si richiede un’analisi di fattibilità che consideri non solo il budget a disposizione, ma la totalità delle risorse tangibili ed intangibili da impiegare nel ciclo ispettivo e manutentivo.
Execution, reporting and performance review
Nel momento in cui il piano di manutenzione proposto rispetta i vincoli di budget e di disponibilità delle risorse, esso viene eseguito. Normalmente gli interventi manutentivi coinvolgono tre tipologie di attività:
1. Interventi preventivi definiti sulla base delle valutazioni RBIM (manutenzione su condizione o programmata);
2. Azioni correttive eseguite in seguito a guasti improvvisi;
3. Guasti identificati mediante il condition monitoring.
In questo contesto si utilizza generalmente la Risk Based Work Selection (RBWS), per assegnare le priorità di intervento su scala giornaliera o settimanale, sia per le azione correttive che per quelle preventive. Ciò è possibile perché nella pratica circa il 40% dei suddetti compiti può essere posticipato per diverse settimane. Perciò, lo strumento proposto consente di selezionare non solo la politica manutentiva ottimale, bensì anche il tempo in cui effettuare l’intervento, tenendo presente che l’allungamento dei tempi di ripristino o di controllo può incrementare il livello di rischio. L’esecuzione dei lavori invece si articola in diverse fasi:
- richiesta di intervento,
- emissione di un ordine di lavoro,
- esecuzione,
- controllo del lavoro eseguito,
- evasione dell’ordine di lavoro,
- registrazione dell’ordine nel sistema informativo.
Per quanto riguarda quest’ultimo punto, le organizzazioni moderne adottano un sistema di gestione della manutenzione computerizzato (CMMS) come strumento chiave per il coordinamento della funzione manutenzione con le altre funzioni aziendali. Tale sistema è costituito tipicamente dai seguenti moduli:
- gerarchia dei guasti delle apparecchiature che costituiscono l’impianto;
- informazioni tecniche;
- piani di manutenzione;
- ordini di lavoro;
- reportistica sugli interventi eseguiti.
In particolare, la registrazione degli interventi eseguiti risulta di primaria importanza per diverse ragioni:
- conoscere la condizione dell’attrezzatura prima e dopo l’intervento manutentivo, in quanto tale informazione consente di migliorare il modello di degrado utilizzato e dunque correggere le stime future in fase di pianificazione;
- controllare i tempi e i costi del lavoro permettendo l’aggiornamento dei parametri riguardanti le risorse impiegate quali: ore di lavoro svolte, parti di ricambio utilizzate, strumenti adottati etc.
Dunque, una reportistica accurata rappresenta la chiave per analizzare ed aggiornare i piani di manutenzione, attraverso una serie di dati riguardanti:
- backlog – ordini non ancora evasi,
- guasti improvvisi,
- disponibilità delle attrezzature oppure perdite legate alle azioni di manutenzione,
- affidabilità dei sistemi di sicurezza,
- tendenze di parametri chiave del processo produttivo e manutentivo connessi all’affidabilità, alla disponibilità ed all’integrità.
A valle del processo di reportistica, è necessario poi considerare le attività di monitoraggio, che consentono di valutare l’efficienza e l’efficacia sia del sistema manutentivo che del sistema produttivo; individuando le criticità che limitano di fatto le prestazioni del sistema nel suo complesso. Dunque, attraverso i risultati del monitoraggio, si possono identificare le aree critiche suscettibili al miglioramento, che possono essere rintracciate sia nel piano manutentivo, compresa la sua esecuzione, che nel piano di produzione. Generalmente la fase di monitoraggio può essere realizzata mediante attività di audit oppure attraverso la definizione di una serie di indicatori di prestazione (Key Performance Indicator). Nel primo caso, gli audit possono essere di tipo interno od esterno; quelli esterni forniscono, come valore aggiunto, la possibilità di avere un giudizio oggettivo sullo stato dell’arte del sistema produttivo. I KPI’s rappresentano invece degli strumenti di misurazione degli scostamenti rispetto agli obiettivi prefissati e possono essere di natura economica, tecnica ed organizzativa. Inoltre possono essere definiti da diversi attori quali: top management, maintenance management o ancora dai tecnici della manutenzione. Poiché l’obiettivo dell’elaborato è quello di valutare gli effetti delle azioni manutentive sulle prestazioni del processo produttivo, risulta importante valutare dei KPI’s che perseguano tale scopo.
VI edizione Safap 2014 - Simulazione dinamica del processo di manutenzione basato sul rischio - a cura di L. C. Santillo, M. Gallo, M. Di Nardo, L. Monica, M. Madonna, F. Giacobbe (Formato pdf, 285 kB).

I contenuti presenti sul sito PuntoSicuro non possono essere utilizzati al fine di addestrare sistemi di intelligenza artificiale.
Per visualizzare questo banner informativo è necessario accettare i cookie della categoria 'Marketing'