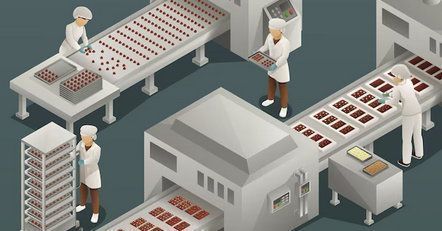
Per utilizzare questa funzionalità di condivisione sui social network è necessario accettare i cookie della categoria 'Marketing'.
Fattori di rischio e prevenzione degli infortuni nell’industria alimentare
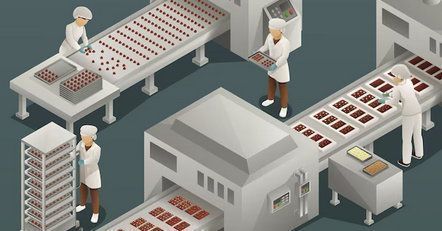
Roma, 19 Dic – Una recente scheda informativa di Infor.MO, il sistema di sorveglianza nazionale degli infortuni mortali e gravi sul lavoro, ha mostrato come nell’industria alimentare un terzo degli infortuni si concentri nella produzione di prodotti da forno e farinacei.
E lo studio evidenzia, inoltre, tre primarie modalità di incidente:
- il contatto con organi lavoratori in movimento (48,2%),
- l’avviamento inatteso/inopportuno di veicolo, macchina o attrezzatura (13,1%)
- la fuoriuscita/contatto con gas, fumi, aerosol e liquidi (8,3%).
Stiamo parlando della scheda 20, dal titolo “ Dinamiche infortunistiche e fattori di rischio nell’industria alimentare” e a cura di A. Guglielmi, M. Pellicci e D. De Merich (Inail, Dimeila), L. Roccatto e S. D’Amico (Azienda Usl di Modena - Servizio prevenzione sicurezza ambienti di lavoro). Il documento, oltre a fornire le caratteristiche descrittive e l'analisi delle dinamiche infortunistiche, si sofferma anche sui fattori di rischio e propone alcune delle possibili misure preventive e protettive da adottare per il controllo e la gestione del rischio infortunistico.
Ricordiamo che l’ industria alimentare (codice C10 della classificazione Ateco 2007) comprende, come ricordato nel documento, diverse attività che “vanno dalla lavorazione/conservazione di carne, pesce, frutta e ortaggi, all’industria lattiero/casearia, alla produzione di panificati e di altri prodotti alimentari, fino a quelli per l’alimentazione degli animali (da allevamento e da compagnia)”.
Dopo aver già fornito informazioni sui dati infortunistici, ci soffermiamo oggi su rischi e prevenzione con riferimento ai seguenti argomenti:
- La scheda n.20 di Informo e i principali fattori di rischio
- Misure preventive e protettive: aspetti procedurali e rischio macchina
La scheda n.20 di Informo e i principali fattori di rischio
La scheda indica che per evidenziare le caratteristiche dei fattori di rischio degli eventi occorsi nell’ industria alimentare “è stata condotta un’analisi puntuale delle informazioni sulle dinamiche infortunistiche registrate nella banca dati del sistema Infor.Mo attraverso il modello di analisi multifattoriale”. E a fronte dei 168 infortuni mortali e gravi selezionati “sono stati rilevati 309 fattori di rischio” distinti nella tabella 3 secondo la categoria di appartenenza.
Riprendiamo dal documento la tabella:
Riguardo ai fattori di rischio al primo posto “compaiono con il 49,9% gli aspetti procedurali (attività infortunato e di terzi), riassumibili in sequenze operative scorrette o usi errati di attrezzatura per pratiche abituali (42,0%), azioni estemporanee (39,5 %) e carenza di informazione/ formazione/addestramento (14,0%)”.
In particolare le criticità registrate nelle modalità lavorative “sono riconducibili ad accessi con macchine e impianti in funzione, a interventi sui sistemi di sicurezza per consentire l’accesso a organi di lavoro ancora in movimento di impianti e macchine in funzione, al mancato riposizionamento/ riattivazione delle protezioni dopo interventi su macchine e impianti, a non utilizzi di accessori di lavoro quali spingitoi, a posizionamenti errati rispetto alle macchine e attrezzature in movimento, a procedure di riavvio dei cicli produttivi senza la verifica e il necessario coordinamento per assicurarsi della non presenza di altri lavoratori in zone di pericolo, ad errori nelle manovre di macchine e impianti di sollevamento e trasporto, ad attività di manutenzione senza l’attivazione delle procedure di sicurezza”.
Riguardo, in particolare, alla categoria delle macchine, attrezzature e impianti implicati negli eventi (“con frequenza superiore alla media di tutti i settori”), si evidenzia la “mancanza di protezioni fisse, mobili e sensibili (43,8%) quali griglie, carter, microinterruttori, barriere immateriali o di accessori di sicurezza quali sistemi di riavvio o tasti di emergenza, l’inadeguatezza dei sistemi di protezione (25,0%) inclusi quelli di messa a terra la rimozione e la modifica dei sistemi di sicurezza (20,8%). Queste sono essenzialmente macchine, attrezzature e impianti di lavorazione dei prodotti da forno, dei farinacei, delle carni, degli ortaggi, ecc”.
Nel fattore Ambiente emergono poi “posti di lavoro o passaggio non adeguatamente protetti contro la caduta di materiale, spazi di manovra e lavoro inadeguati, assenza di segnaletica, carenze dei sistemi di aspirazione e ventilazione, ambienti con caratteristiche di sicurezza Atex insufficienti”. Mentre i problemi di sicurezza registrati per i DPI “sono riconducibili principalmente al non utilizzo di DPI quali guanti, grembiuli, sistemi di protezione delle vie respiratorie e dispositivi di imbrago anche per il recupero in emergenza, per pratiche abituali, carenza di formazione e in misura inferiore per la mancata fornitura degli stessi”.
Infine per la categoria dei materiali “ricorre lo stoccaggio non adeguato per modalità (es. big bag stoccati uno sull’altro e non su adeguate superfici) e per tipologia di contenitori usati allo scopo (non etichettati o di tipo alimentare per contenere agenti chimici pericolosi)”.
Un aspetto importante riguarda poi la valutazione dei rischi.
Si indica che dei 309 fattori di rischio rilevati in fase di indagine “l’83,6% dei fattori di rischio (al netto del dato mancante) risulta essere stato valutato in modo inadeguato all’interno dell’azienda”.
E riguardo alle tre primarie modalità di incidente, indicate in apertura di articolo:
- per il contatto con organi lavoratori in movimento “predominanti e quasi esclusive sono le criticità procedurali (51,7%) e delle attrezzature di lavoro (45,5%), presenti contemporaneamente quali fattori di rischio nei 3/4 degli infortuni analizzati”;
- “nell’avviamento inatteso/inopportuno di macchine e impianti sono frequenti criticità delle pratiche lavorative dell’infortunato (41,3%) ma anche di terzi (15,2%) collegate in particolare al coordinamento tra i componenti delle squadre di lavoro, seguite poi da problematiche riscontrate nelle macchine ed attrezzature di lavoro in uso (34,8%). Errori procedurali e impianti macchine attrezzature non sicure sono presenti contemporaneamente nel 68,2% dei casi registrati negli avviamenti intempestivi”;
- nella “fuoriuscita/contatto con gas, fumi, aerosol e liquidi pericolosi si evidenziano essenzialmente modalità operative errate del lavoratore che si infortuna (40,0%), problemi delle macchine e attrezzature di lavoro (24,0%) e non uso o non fornitura dei necessari DPI (24,0%)”.
Misure preventive e protettive: aspetti procedurali e rischio macchina
Chiaramente, indica la scheda, “la conoscenza dei fattori di rischio, in particolare delle cause infortunistiche con conseguenze più gravi, e la corretta valutazione del rischio sono fondamentali per garantire la sicurezza e la salute dei lavoratori e per individuare e adottare le misure preventive e protettive più adeguate”.
Se tra le cause degli infortuni analizzati emergono gli aspetti procedurali correlabili all’attività lavorativa, la “definizione e l’adozione di procedure di lavoro sicure, dettagliate per ogni attività, costituisce una delle misure di prevenzione da adottare”. E ciò implica “un’adeguata formazione e informazione su come svolgere nel modo più sicuro le diverse attività e uno specifico addestramento sull’utilizzo corretto delle attrezzature”.
Inoltre il controllo e la supervisione delle varie attività, “assicurando la necessaria vigilanza per intervenire e porre rimedio a situazioni di potenziale pericolo, sono importanti per evitare l’insorgenza e l’adozione di abituali e non corrette pratiche lavorative. Anche il riconoscimento e la valorizzazione dei ruoli a ciò demandati (es. preposto) garantiscono l’effettiva applicazione delle procedure di lavoro e l’utilizzo corretto delle attrezzature da parte dei lavoratori”.
Veniamo invece ai problemi connessi alle macchine e attrezzature in uso.
Si indica che è fondamentale assicurarsi che “le stesse vengano utilizzate all’interno di un ambiente adeguato per dimensioni e dotazione di impianti”. E l’uso di macchine e attrezzature di lavoro “deve essere conforme alle istruzioni del fabbricante ed è necessario verificarne sempre l’utilizzo per gli usi previsti e nei modi indicati nel manuale di uso e manutenzione. Ogni differente impiego deve essere vietato”.
Inoltre:
- “le macchine e le attrezzature di lavoro devono essere oggetto di periodici controlli e manutenzione sia per garantirne il regolare funzionamento nel tempo, sia per accertare la presenza ed il corretto posizionamento e l’efficacia dei ripari e dei dispositivi di sicurezza previsti dal fabbricante. Utile strumento è il registro dei controlli la cui corretta compilazione deve essere oggetto di supervisione”;
- “in caso di incidente o malfunzionamento di una macchina o di un’attrezzatura di lavoro, seguire le corrette procedure di emergenza preventivamente definite e comunicate. Le procedure possono includere l’arresto immediato della macchina, l’allontanamento dall’area di lavoro e l’isolamento della macchina dall’alimentazione elettrica”;
- “ove previsto l’utilizzo di DPI questi dovranno essere adeguati ai rischi da prevenire e scelti in modo da non comportare di per sé un rischio maggiore, tenendo conto delle esigenze ergonomiche o di salute del lavoratore”;
- “in relazione alle principali modalità incidentali per limitare la possibilità di contatti con parti meccaniche in movimento proteggere o segregare le aree operative con barriere fisiche e/o con dispositivi di sicurezza interbloccati”;
- “posizionare nei pressi delle protezioni la cartellonistica indicante la presenza di organi rotanti in movimento, il divieto di rimuovere le protezioni e di effettuare regolazioni e manutenzioni con organi in movimento”;
- “nel caso in cui sia necessario, per esigenze comunque previste dal fabbricante, effettuare operazioni con organi in movimento, adottare misure alternative di riduzione del rischio (ad es. procedure ed istruzioni operative) garantendo adeguata formazione e vigilanza sulla loro corretta applicazione”.
In merito agli avviamenti inattesi o intempestivi dei cicli lavorativi di macchine o attrezzature durante la manutenzione o l’ordinario utilizzo si sottolinea poi di “dotare il macchinario di dispositivi di comando e sicurezza visibili ed identificabili, protetti contro l’azionamento accidentale, implementare la chiusura a chiave dei quadri di azionamento con tenuta della chiave da parte dell’operatore che svolge attività di manutenzione (lock out) utilizzando adeguata cartellonistica di avvertimento (tag out) e attivare opportuni protocolli di manutenzione delle apparecchiature”.
Per prevenire poi la fuoriuscita/contatto con gas, fumi, aerosol e liquidi pericolosi “utilizzare barriere fisiche, sistemi di aspirazione localizzata, di ventilazione e/o fornire equipaggiamento di protezione individuale adeguato”.
Inoltre è importante “redigere un piano di emergenza che includa la formazione del personale su come gestire le situazioni di emergenza e l’accesso all’equipaggiamento di protezione e di soccorso in caso di fuoriuscita o di contatto con agenti pericolosi”.
La scheda ricorda poi che particolare attenzione dovrà essere rivolta “alle procedure per la pulizia, sanificazione o disinfezione delle macchine, attrezzature o superfici limitando il più possibile l’esposizione ad agenti pericolosi la cui scelta dovrà essere oggetto di attenta valutazione per limitare i rischi. Nel caso le operazioni di igienizzazione dovessero riguardare parti in movimento o prossime alle stesse e per ragioni operative non sia possibile arrestarne il moto, operare a distanza di sicurezza e con ausili tali da ridurre al minimo il rischio di contatto o trascinamento”.
Riguardo alle altre modalità di accadimento degli infortuni, in particolare durante la manutenzione di impianti o strutture in altezza, è importante “garantire le misure di protezione da cadute dall’alto dell’infortunato, collettive e/o individuali e, per la caduta dall’alto di gravi, fornire attrezzature ancorabili, prevedere segnalazioni fisse o mobili nelle aree di movimentazione di materiali, interdire il passaggio e lo stazionamento delle persone nelle zone pericolose e prevedere se necessario l’utilizzo di movieri”.
Infine per la riduzione del rischio di investimento, presente anche nell’ industria alimentare, “predisporre percorsi pedonali separati da quelli veicolari e dalle aree di movimentazione automatizzata dei prodotti. Le vie di circolazione interne all’azienda devono essere di ampiezza adeguata e delimitate mediante segnaletica”.
Un ultimo aspetto trattato nella scheda si segnala che negli ambienti di lavoro particolarmente rumorosi “è opportuno programmare un piano aziendale di riduzione del rumore (es. interventi di bonifica acustica, sostituzione delle sorgenti di rumore con altre aventi minore emissione sonora, ecc.)”.
Concludiamo rimandando alla lettura integrale della scheda che riporta anche analisi sui dati e le dinamiche infortunistiche, che presenta diversi grafici esplicativi e che riporta, infine, informazioni, su bibliografia e sitografia, utili per ulteriori approfondimenti sul tema.
Tiziano Menduto
Scarica il documento da cui è tratto l'articolo:
Infor.mo., Sistema di sorveglianza degli infortuni mortali e gravi, “ Dinamiche infortunistiche e fattori di rischio nell’industria alimentare”, scheda n. 20, a cura di A. Guglielmi, M. Pellicci e D. De Merich (Inail, Dimeila), L. Roccatto e S. D’Amico (Azienda Usl di Modena - Servizio prevenzione sicurezza ambienti di lavoro), edizione 2023 (formato PDF, 595 kB).
Vai all’area riservata agli abbonati dedicata a “ Dinamiche infortunistiche e prevenzione nell’industria alimentare”.

I contenuti presenti sul sito PuntoSicuro non possono essere utilizzati al fine di addestrare sistemi di intelligenza artificiale.
Per visualizzare questo banner informativo è necessario accettare i cookie della categoria 'Marketing'