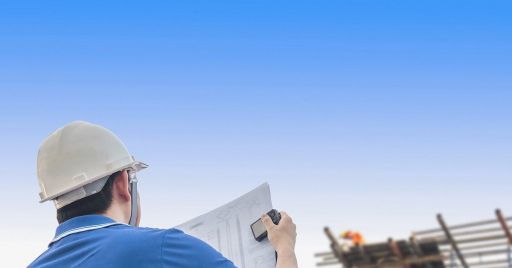
Per utilizzare questa funzionalità di condivisione sui social network è necessario accettare i cookie della categoria 'Marketing'.
Sicurezza e tutela della salute nell’esecuzione dei Micropali
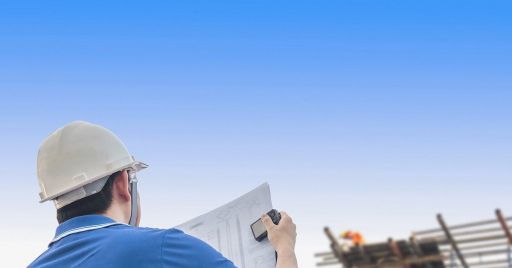
Ancora oggi, nonostante siano passati quindici anni dall’entrata in vigore del D. Lgs. n° 81/2008 con il suo allegato XV, si continuano a vedere PSC assolutamente carenti dal punto di vista qualitativo; prevalentemente le carenze riguardano la superficialità e l’approssimazione con cui viene effettuata la ricerca di tutte quelle scelte prevenzionali (progettuali, tecniche e organizzative) in grado di eliminare, quando possibile, o ridurre al minimo i rischi per il personale incaricato dell’esecuzione dei lavori.
D’altra parte, è indubbiamente vero che un’efficace analisi prevenzionale in fase progettuale può essere condotta solo se vi è una buona conoscenza dei processi costruttivi che si svolgeranno in cantiere.
Se per alcune tipologie costruttive quest’affermazione può sembrare scontata, per altre non lo è per nulla. Infatti, esistono tutta una serie di lavorazioni, veramente complesse, la cui conoscenza è tutt’altro che diffusa.
Quindi, nel seguito di questo contributo, verranno affrontate le problematiche inerenti alla sicurezza e la tutela della salute nella progettazione ed esecuzione dei micropali, in modo da fornire agli addetti ai lavori una serie di informazioni utili per la redazione del piano di sicurezza e coordinamento relativo ad appalti che includono questa tipologia di lavorazione.
Pubblicità
Cosa sono e a cosa servono i “micropali”
Per “Micropalo” s’intende un palo trivellato di diametro inferiore a 300 mm, il cui fusto è costituito da malta o miscela cementizia iniettata in opera e da un’armatura costituita generalmente da un tubo o profilato metallico
Il micropalo può essere assoggettato a sollecitazioni di compressione, trazione e taglio, e può essere verticale, orizzontale o inclinato.
Per quanto riguarda l’applicazione, i micropali possono essere utilizzati per:
- il consolidamento di fondazioni di tipo diretto come le travi rovesce, le platee, i plinti, ecc.;
- gli interventi di riparazione/ripristino di fondazioni danneggiate da infiltrazioni di acque o da filtrazione ed erosione del terreno di fondazione;
- il consolidamento del terreno al fine di migliorare le caratteristiche fisico-meccaniche prima di eseguire le fondazioni dirette;
- la realizzazione di paratie chiamate in gergo "berlinesi», eseguite, prevalentemente, in ambiente urbano.
I micropali si possono, poi, differenziare in base allo scopo progettuale:
- micropali caricati direttamente, armatura in grado di resistere alla maggior parte del carico applicato;
- elementi di rinforzo del terreno per ottenere un sistema composito rinforzato micropali/terreno in grado di resistere ai carichi esterni applicati.
La tecnica adottata dovrà essere scelta in funzione della possibilità di raggiungere i requisiti di resistenza ed affidabilità previsti.
La perforazione è solitamente a rotazione con carotaggio continuo o a rotopercussione.
Come fluidi di circolazione si adottano fanghi bentonitici o aria per lo scavo in roccia.
Le attrezzature di lavoro normalmente utilizzate per l’esecuzione dei micropali, sono le seguenti:
- macchine di perforazione quali sonde di perforazione e relative attrezzature di supporto (aste di perforazione, rivestimenti metallici, pompe, ecc.)
- attrezzature ausiliarie quali impianti di miscelazione ed iniezione, pompe, compressori d’aria, ecc..
- attrezzature di supporto quali escavatori, pale, terne, camion, ecc.
Scelte progettuali ed organizzative per eliminare o ridurre i rischi
Durante l’esecuzione di questa particolare lavorazione, l’attività eseguita è potenzialmente in grado di trasmettere all’ambiente circostante, i seguenti rischi:
- rumore, polveri, gas di scarico, ecc.;
- franamento e/o crollo del terreno con conseguente rischio per terzi e per servizi esistenti (vie di comunicazione, sottoservizi, linee elettriche aeree, ecc.);
- caduta di gravi al di fuori dell'area di cantiere;
- interferenze con vie di comunicazione (strade, ferrovie, ecc.);
- vibrazioni con conseguenti cedimenti e lesioni strutturali ad edifici/servizi limitrofi.
- lo "stato di consistenza" delle strutture limitrofe all'area interessata dall'esecuzione dei lavori attraverso specifiche indagini;
- la definizione d’idonei sistemi di monitoraggio nel caso in cui fosse ci fosse il rischio di alterare la statica delle strutture limitrofe e la relativa periodicità dei controlli;
- le modalità di accesso all'area di lavoro delle macchine e delle attrezzature necessarie per l'esecuzione dei lavori tenendo conto delle caratteristiche del sito e delle modalità di trasporto e di assemblaggio sul cantiere, delle dimensioni, dei pesi, degli spazi necessari per il montaggio e la messa in opera, ecc.;
- i criteri per minimizzare l'impatto, di cui al punto precedente, sulle vie interessate dal passaggio dei mezzi e delle attrezzature da e per il cantiere, sugli edifici, sulle strade, ferrovie, ecc. in esercizio, eventualmente adiacenti alla zona di transito e di lavoro (scelta percorsi, spazi di manovra, separazioni, segnalazioni, ecc.);
- le misure atte a limitare il rischio cadute di gravi al di fuori dell'area di cantiere (posizione macchina, posizione braccio di perforazione, segnaletica, recinzione, ecc.);
- il sistema per minimizzare la trasmissione di polveri e dei gas di scarico all'ambiente circostante durante le fasi di preparazione del piano di lavoro con macchine movimento terra;
- le misure tecniche, organizzative e procedurali per minimizzare il disturbo, nel caso in cui la valutazione preventiva delle emissioni di rumore evidenzi il superamento dei limiti imposti per la zona in cui è ubicato il cantiere.
- lavorare nelle, vicinanze di sottoservizi, linee elettriche aeree, strade, ferrovie, ecc.;
- eseguire le operazioni di accesso dei mezzi di trasporto delle attrezzature, dello scarico, del montaggio e delle verifiche prima dell'inizio dei lavori delle attrezzature stesse;
- evitare la caduta di gravi al di fuori dell'area di cantiere;
- minimizzare le emissioni di polveri, gas e rumore.
Durante l’esecuzione di questa particolare lavorazione, è possibile si concretizzino dei rischi derivanti dalle interferenze tra attività lavorative in atto nel sito interessato dai lavori (caduta di gravi, incidenti tra macchine operatrici, ecc.).
- la valutazione preventiva delle interferenze plano-altimetriche tra le attività di preparazione del piano di lavoro con le macchine movimento terra ed il posizionamento della macchina di perforazione e/o con altre attività lavorative che si svolgono nel sito;
- la sequenza delle sottofasi di lavoro (se non fosse possibile eliminare le interferenze citate), al fine di minimizzare i rischi connessi alla coesistenza delle stesse nel sito, individuando le conseguenti misure tecniche, organizzative e procedurali necessarie.
Durante l’esecuzione di questa particolare lavorazione, è possibile si concretizzino dei rischi derivanti dalle caratteristiche del sito quali:
- franamento/crollo del terreno con conseguente rischio di schiacciamento/seppellimento degli addetti;
- contatto/inalazione con/di sostanze/gas inquinanti/pericolosi presenti nel terreno;
- contatto con linee elettriche aeree o sottoservizi (linee elettriche, gas, acqua, ecc.) durante le varie fasi di lavoro;
- interferenze con servizi esistenti (strade, ferrovie, ecc.).
Per far fronte ai rischi derivanti, dalle caratteristiche del sito, il progettista e il CSP dovrebbero effettuare precise scelte progettuali ed organizzative riguardanti:
- la preventiva valutazione delle caratteristiche geomeccaniche del sito al fine di verificare la sussistenza di una portanza adeguata al peso delle macchine che vi dovranno operare;
- gli idonei interventi in grado di assicurare la stabilità delle macchine durante lo svolgimento dell’attività lavorativa prevista (riporti di terreno, gradonature, sistemi di ridistribuzione del carico delle macchine sul terreno, ecc.), in caso di caratteristiche geomeccaniche non adeguate;
- le indagini per escludere con certezza la presenza di materiali o sostanze inquinanti dannose per la salute degli addetti e, in caso contrario, l’individuazione degli interventi da attuare nel caso in cui, durante le fasi di lavoro, si manifesti la presenza di materiali o sostanze dannose per la salute (sistemi di monitoraggio/controllo, procedure di sicurezza, modalità di allontanamento, deposito e smaltimento);
- i criteri e le modalità di esecuzione delle lavorazioni, nel caso in cui le attività lavorative debbano essere eseguite nelle adiacenze o lungo strade o linee ferroviarie, tenendo conto anche delle specifiche norme che vincolano tali attività in queste particolari situazioni (codice stradale, regolamento ferroviario, ecc.);
- l’individuazione preventiva di linee elettriche o telefoniche aeree nella zona interessata dai lavori;
- l’individuazione preventiva di sottoservizi nella zona interessata dai lavori;
- la predisposizione di una planimetria aggiornata, da allegare al PSC, indicante la posizione delle linee aeree e dei sottoservizi;
- la valutazione della possibilità di mettere fuori servizio le linee aeree e i sottoservizi, contattando preventivamente gli enti proprietari/gestori degli stessi;
- I criteri, le modalità di segnalazione e i sistemi di protezione delle linee aeree e dei sottoservizi nonché le modalità per eseguire i lavori nelle immediate vicinanze.
- eliminare il rischio di perdita di stabilità delle MMT e delle macchine di perforazione;
- definire le modalità di spostamento delle macchine di perforazione nelle aree di lavoro;
- garantire l'incolumità del personale di supporto durante la preparazione dei piani di lavoro ed il posizionamento delle macchine di perforazione (posizione addetti, distanze, ecc.);
- contenere il rischio derivante dalla presenza di materiali/sostanze pericolose per la salute del personale presente;
- lavorare nelle vicinanze di sottoservizi, linee elettriche aeree, strade, ferrovie, ecc..
Durante la fase di preparazione del piano di lavoro e posizionamento della macchina di perforazione, è possibile si concretizzino i seguenti rischi:
- ribaltamento delle macchine MMT durante la fase di preparazione dei piani di lavoro;
- rottura di componenti delle macchine con caduta/fuoriuscita di gravi/fluidi in pressione;
- perdita di stabilità della macchina adibita alla perforazione durante le fasi di posizionamento;
- urti/colpi/impatti/investimenti da parte delle macchine in fase di posizionamento.
Per far fronte a questa tipologia di rischi, il progettista e il CSP dovrebbero effettuare precise scelte progettuali ed organizzative riguardanti:
- la pianificazione delle sequenze lavorative delle macchine MMT addette alla formazione dei piani di lavoro;
- l’individuazione e il dimensionamento, in funzione dell’evoluzione dei lavori, delle possibili aree di accumulo del terreno di risulta in attesa dell’allontanamento dal sito;
- il dimensionamento (resistenza, pendenza, spazio disponibile) dei piani di lavoro che ospiteranno la macchina di perforazione (per la macchina e per il terreno scavato) e per il posizionamento delle batterie d’aste per la perforazione nonchè per l’accesso dei mezzi adibiti al carico ed all’allontanamento del terreno di risulta;
- l’individuazione del percorso ottimale che la macchina di perforazione deve compiere per eseguire la progressiva perforazione ed iniezione;
- l’individuazione del percorso ottimale per gli eventuali mezzi di trasporto del materiale di risulta;
- la definizione dei criteri da adottare, durante gli spostamenti ed il posizionamento della macchina di perforazione nelle aree di lavoro, per evitare contatti accidentali con la macchina stessa o per evitare di essere colpiti da gravi caduti dal braccio (bulloni, viti, ecc.) o, ancora, per evitare spruzzi da fluidi in pressione per eventuale rottura dei circuiti idraulici della macchina di perforazione.
Nel PSC, conseguentemente, dovranno essere richieste specifiche procedure complementari e di dettaglio da esplicitare nel POS riguardo le modalità operative adottate per:
- eseguire le operazioni di accesso dei mezzi di trasporto delle attrezzature, dello scarico, del montaggio e delle verifiche prima dell'inizio dei lavori delle attrezzature stesse;
- eliminare il rischio di perdita di stabilità delle MMT e delle macchine di perforazione;
- definire le modalità di spostamento delle MMT e delle macchine di perforazione nelle aree di lavoro;
- garantire l'incolumità del personale di supporto durante la preparazione dei piani di lavoro ed il posizionamento delle macchine di perforazione (posizione addetti, distanze, ecc.);
- effettuare il posizionamento sull'asse di scavo della macchina di perforazione.
Durante la fase di perforazionesono presenti i seguenti rischi:
- perdita di stabilità della macchina adibita alla perforazione;
- rottura di componenti delle macchine con caduta/fuoriuscita di gravi/fluidi idraulici in pressione;
- urti/colpi/impatti/investimenti da parte delle attrezzature di perforazione;
- ferite e traumi durante il montaggio e lo smontaggio delle aste di perforazione;
- ferite e lesioni durante gli spostamenti in piano;
- proiezione di detriti durante la perforazione.
Per far fronte a questa tipologia di rischi, il progettista e il CSP dovrebbero effettuare precise scelte progettuali ed organizzative riguardanti:
- la pianificazione delle sequenze lavorative della macchina di perforazione;
- la definizione dei criteri che il personale deve seguire per evitare contatti accidentali con la macchina di perforazione;
- l’individuazione e il dimensionamento, in funzione dell'evoluzione dei lavori, delle aree da adibire al deposito temporale delle aste di perforazione;
- l’individuazione, nel caso la perforazione debba essere eseguita in zone con forti pendenze, delle protezioni da adottare per prevenire eventuali franamenti del terreno a monte ed a valle della piazzola di perforazione, tenendo conto anche degli eventi atmosferici in grado di alterare l’equilibrio del terreno (forti precipitazioni con dilavamenti, ecc.);
- la definizione del percorso ottimale per gli eventuali mezzi di trasporto del materiale di approvvigionamento per la perforazione (aste di perforazione, pompe, ecc.);
- la definizione dei criteri da adottare, durante la perforazione, per evitare contatti accidentali con la macchina stessa o per evitare di essere colpiti da gravi caduti dal braccio (bulloni, viti, ecc.) o, ancora, per evitare spruzzi da fluidi in pressione per eventuale rottura dei circuiti idraulici della macchina di perforazione.
Nel PSC, conseguentemente, dovranno essere richieste specifiche procedure complementari e di dettaglio da esplicitare nel POS riguardo le modalità operative adottate per:
- l’esecuzione della perforazione;
- il mantenimento della stabilità delle aree di perforazioni (riporti, allontanamento fango, protezioni contro i franamenti, ecc.);
- l’esecuzione delle manovre di smontaggio/disserraggio delle aste in caso di blocco delle stesse.
- ferite e lesioni durante la predisposizione dell’impianto di miscelazione
- lesioni oculari e cutanee dovuti a schizzi, spruzzi di miscela cementizia
- cadute in piano, cadute all’interno dei mescolatori, urti contro componenti dell’impianto
- cadute dall’alto dai silos di cemento e dai serbatoi.
Per far fronte a questa tipologia di rischi, il progettista e il CSP dovrebbero effettuare precise scelte progettuali ed organizzative riguardanti:
- l’ubicazione funzionale e sicura dell’impianto di miscelazione, tenendo conto degli spazi necessari per posizionare tutti i componenti di un impianto d’iniezione (vasconi, pompe, miscelatori, agitatori, silos, tubazioni, ecc.);
- la previsione degli spazi necessari ai mezzi di trasporto per avvicinarsi all’impianto ed effettuare l’approvvigionamento dei silos di cemento;
- la definizione dell’andamento planimetrico della tubazione in pressione e delle relative protezioni contro il danneggiamento meccanico e contro la fuoriuscita accidentale di miscela cementizia.
Nel PSC, conseguentemente, dovranno essere richieste specifiche procedure complementari e di dettaglio da esplicitare nel POS riguardo le modalità operative adottate per:
- l’installazione dell’impianto di miscelazione ed iniezione;
- la preparazione e l’invio alla sonda della miscela cementizia in pressione;
- la gestione di eventuali situazioni di emergenza (malfunzionamenti impianto, ecc.).
Nella fase di messa in opera dei micropali, sono presenti i seguenti rischi:
- rischio di schiacciamento per perdita di stabilità della macchina di perforazione;
- caduta e/o proiezione di gravi/fluidi idraulici in pressione per rottura di componenti delle macchine di perforazione;
- rischio da MMC durante la messa in opera dei micropali;
- cadute in piano/scivolamenti nelle aree di lavoro per presenza di fango.
Per far fronte a questa tipologia di rischi, il progettista e il CSP dovrebbero effettuare precise scelte progettuali ed organizzative riguardanti:
- il dimensionamento degli spazi di lavoro necessari per l’approvvigionamento e lo stoccaggio dei micropali prima del loro inserimento;
- il dimensionamento degli spazi di lavoro necessari per effettuare l’inserimento dei micropali nei fori eseguiti, tenendo conto delle loro dimensioni (peso, lunghezza, diametro, ecc.);
- l’impiego di sistemi di sollevamento meccanici necessari (gruette, argano sonda, ecc.) per l’inserimento dei micropali nei fori eseguiti per ridurre il rischio da MMC;
- il sistema di protezione da utilizzare per evitare che gli spezzoni sporgenti dal terreno dei micropali posizionati nei fori, possano causare rischi per gli addetti.
Nel PSC, conseguentemente, dovranno essere richieste specifiche procedure complementari e di dettaglio da esplicitare nel POS riguardo le modalità operative adottate per:
- lo stoccaggio dei micropali prima di procedere al loro inserimento nei fori eseguiti;
- il sollevamento, il trasporto e la messa in opera dei micropali;
- la segnalazione della posizione dei micropali e le protezioni adottate per diminuire il rischio conseguente alla presenza degli spezzoni dei micropali sporgenti nell’area di lavoro.
Durante la fase di lavoro riguardante l’iniezione dei micropali, si possono concretizzare i seguenti rischi:
- rischio di schiacciamento per perdita di stabilità della macchina;
- caduta e/o proiezione di gravi/fluidi idraulici in pressione per rottura di componenti delle macchine di perforazione;
- fuoriuscita di miscela cementizia in pressione con rischio di lesioni e traumi per gli addetti;
- ferite e traumi durante il posizionamento del pistoncino e delle cannette d’iniezione e la successiva iniezione;
- cadute in piano/scivolamenti nelle aree di lavoro per presenza di fango.
Per far fronte a questa tipologia di rischi, il progettista e il CSP dovrebbero effettuare precise scelte progettuali ed organizzative riguardanti:
- la definizione del tracciato delle tubazioni per l’invio della miscela cementizia alle zone d’iniezione;
- la previsione di un sistema per evitare o ridurre al minimo la formazione e l’accumulo di fanghi derivanti dall’attività di iniezione in pressione per la realizzazione della guaina e/o del bulbo dei micropali (pompe di aggottamento, vasche di raccolta, ecc.).
Nel PSC, conseguentemente, dovranno essere richieste specifiche procedure complementari e di dettaglio da esplicitare nel POS riguardo le modalità operative adottate per:
- il posizionamento della linea in pressione dall’impianto alla macchina di perforazione ed iniezione;
- le modalità di iniezione dei micropali;
- il sistema adottato per evitare la formazione e lo spargimento di fanghi effluenti dalla perforazione ed iniezione.
- le modalità di esecuzione degli interventi di manutenzione in caso di occlusione della linea, del pistoncino d’iniezione o di malfunzionamento dell’impianto.
Carmelo G. Catanoso
Ingegnere Consulente di Direzione

I contenuti presenti sul sito PuntoSicuro non possono essere utilizzati al fine di addestrare sistemi di intelligenza artificiale.
Per visualizzare questo banner informativo è necessario accettare i cookie della categoria 'Marketing'