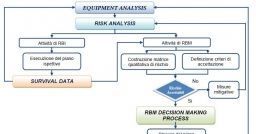
Per utilizzare questa funzionalità di condivisione sui social network è necessario accettare i cookie della categoria 'Marketing'
Questo articolo è pubblicato sotto una Licenza Creative Commons.
Per visualizzare questo banner informativo è necessario accettare i cookie della categoria 'Marketing'
System Dynamics: modellazione e simulazione dei rischi
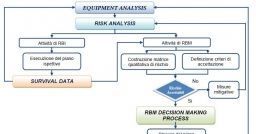
Pubblichiamo la seconda parte della relazione “Simulazione dinamica del processo di manutenzione basato sul rischio” presentata in occasione della VI edizione Safap che spiega l’utilizzo della logica della System Dynamics (SD) che, nell’ambito della valutazione e gestione del rischio, sta assumendo un ruolo sempre più importante come strumento di modellazione esimulazione.
La prima parte metteva in evidenzia come la pianificazione della manutenzione possa contribuire significativamente alla minimizzazione del rischio e diventare un’attività strategica nella gestione del rischio di un’organizzazione.
L. C. Santillo, M. Gallo, M. Di Nardo, L. Monica, M. Madonna, F. Giacobbe
La logica della System Dynamics per la pianificazione RBIM e costruzione del Causal Loop Diagram
L’approccio System Dynamics
Nella valutazione e nella gestione del rischio, un ruolo sempre più importante è stato assunto da strumenti quali la modellazione e la simulazione, destinati a supportare decisioni di carattere strategico ed a favorire l’evoluzione dei modelli mentali degli attori aziendali. Per tale motivo si è sviluppata una logica, nota come System Dynamics, la quale offre potenzialità che altri strumenti informativi e di simulazione, in passato, hanno rivelato di non possedere. In un’ottica aziendale, questo approccio costituisce e fornisce una chiave di lettura della realtà, caratterizzandosi come strumentazione di interpretazione delle modalità con cui le politiche e le decisioni degli attori organizzativi influenzano la struttura del sistema di riferimento, incidendo sulle dinamiche delle risorse a disposizione.
Dal punto di vista formale, la System Dynamics (SD) è un approccio allo studio del comportamento dei sistemi complessi caratterizzati da meccanismi di feedback, in cui si enfatizza il ruolo dell’intreccio tra politiche, strutture decisionali e ritardi temporali; che influenzano i fenomeni dinamici. Le analisi e le interpretazioni del comportamento dei sistemi sviluppate nell’ambito della SD si fondano su due concetti:
- la divisione tra variabili di stato (livello/stock) e la dinamica di queste (flow);
- la presenza di circuiti di retroazione (feedback loop).
L’analisi condotta nell’ambito della SD quindi, si ancora a due ipotesi fondamentali. Da una parte, si postula che dall’intreccio di processi decisionali, flussi informativi e relazioni interpersonali all’interno delle aziende, emergano strutture costituite da circuiti di retroazione concatenati. In secondo luogo, la SD ipotizza che i comportamenti dei sistemi siano la conseguenza delle caratteristiche strutturali che assumono tali aggregazioni, che regolano il “tasso” (rate) di accumulazione o erosione delle variabili livello (stock) in essi compresi. L’aspetto più interessante risiede nel fatto che la System Dynamics ha una logica estremamente pragmatica. Infatti, l’enfasi non è posta sulla capacità del modello di prevedere particolari stati puntuali del sistema o sul rigore con cui le ipotesi del modello sono state testate empiricamente, bensì sulla possibilità di comprendere la logica con cui le variabili rilevanti interagiscono, il ruolo che ciascuna di essa gioca, i punti in cui il sistema è sensibile agli interventi e gli scenari che emergono come conseguenza di ipotesi alternative circa lo stato iniziale del sistema.
La metodologia prevede una serie di fasi che possono essere riassunte nei seguenti punti:
- identificazione di un problema;
- sviluppo di ipotesi dinamiche e mappe causali per spiegare la causa del problema;
- costruzione al computer di un modello di simulazione che rappresenti il sistema alla radice del problema;
- test del modello per verificare che sia in grado di riprodurre il comportamento osservato nel mondo reale;
- elaborazione e test nel modello di politiche alternative finalizzate ad alleviare il problema;
- implementazione della soluzione ottimale.
In particolare, la fase di simulazione rappresenta il momento centrale dell’intera metodologia in quanto è un processo mediante il quale viene rappresentato il comportamento di un sistema reale e la sua dinamica nel tempo, valutando, mediante sperimentazioni, la reazione del sistema a stimoli esterni e interni differenti. In campo aziendale, la simulazione rappresenta una vera e propria metodologia decisionale con cui si analizzano le caratteristiche di un sistema reale, al fine di comprenderne i meccanismi di funzionamento necessari per prevedere il suo sviluppo futuro e per mettere a punto le più opportune linee di comportamento. Dunque, i modelli di simulativi consentono di valutare a priori le prestazioni ottenibili dal sistema considerato prima ancora di procedere alla sua realizzazione o modifica. In questo modo è possibile prevedere il comportamento del sistema al variare di condizioni e parametri, valutare tutti gli indicatori di performance tecnici ed economici, trovare le soluzioni più opportune riducendo i costi di investimento e di esercizio, limitando i rischi. Numerose sono le simulazioni realizzabili, riferite sia al sistema aziendale inteso complessivamente, sia a singole parti opportunamente definite, finalizzate a supportare i processi decisionali ai vari livelli organizzativi. In generale non esistono vincoli o restrizioni nella scelta del campo di applicazione della simulazione.
Gli strumenti della System Dynamics
Nell’ambito della SD vengono utilizzati una serie di strumenti attraverso cui è possibile:
• Aumentare la consapevolezza sulle caratteristiche dinamiche dei sistemi di riferimento;
• Formalizzare le conoscenze e le informazioni disponibili;
• Sviluppare idonee politiche e testare le decisioni prese affrontando diversi scenari gestionali;
• Supportare un processo di apprendimento in ciascuna delle suddette situazioni.
Gli strumenti fondamentali dalla cui aggregazione ha origine la struttura di un sistema dinamico sono sostanzialmente due: i Causal Loop Diagram e gli Stock and Flow Diagram. In questo lavoro ci si è concentrati maggiormente sull’analisi e definizione del Causal Loop Diagram (CLD). Tali diagrammi rappresentano le mappe grafiche atte ad individuare la struttura causale del sistema di riferimento, che, nel caso di specie, sono stati realizzati mediante l’ausilio di un software Open Source (Vensim).
Causal Loop Diagram
In generale, i Causal Loop Diagrams (CLD), costituiscono delle mappe grafiche atte a rappresentare, in maniera semplice ed immediata, la struttura causale del sistema di riferimento. Nel dettaglio, un CLD permette di esplicitare e formalizzare le relazioni causali che legano un insieme di variabili appartenenti al medesimo sistema di riferimento, individuando in tal modo i meccanismi di feedback attivi all’interno del sistema in esame e le dinamiche relative. In tal senso, i CLD dimostrano di essere degli strumenti estremamente efficaci in quanto:
- rappresentano un primo approccio di carattere puramente grafico al problema indagato, permettendone una descrizione ed interpretazione preliminare basata su un’impostazione estremamente intuitiva;
- modellano sinteticamente ed efficacemente le ipotesi elaborate in relazione alle cause ritenute alla base delle dinamiche analizzate;
- sono idonei ad esplicitare, approfondire e formalizzare i modelli mentali degli attori aziendali coinvolti;
- favoriscono il processo comunicativo e di condivisione delle conoscenze tra gli appartenenti ad una medesima realtà aziendale.
In riferimento al primo punto è importante sottolineare che l’approccio grafico costituisce il primo dei due steps con i quali si articola il processo simulativo; la seconda fase è rappresentata invece dal passaggio, dal diagramma causale (che fornisce ovviamente una rappresentazione qualitativa del modello) al diagramma di flusso vero e proprio che, invece, costituisce l’essenza del modello quantitativo.
In definitiva, è possibile affermare che un CLD rappresenta uno strumento concettuale estremamente utile nell’individuazione e formalizzazione di un processo di tipo dinamico, all’interno del quale gli effetti di una singola causa sono individuati e tracciati attraverso una serie di variabili fino alla medesima causa di origine.
In tali diagrammi, tuttavia, il vero valore aggiunto si ottiene quando è possibile legare tra di
loro due o più variabili in maniera tale che esse formino un ciclo chiuso, o loop. Questi loop possono essere principalmente di due tipi:
- loop di rinforzo: in questo caso essi portano ad un’espansione o viceversa ad un abbattimento reciproco dei valori assunti dalle variabili connesse;
- loop di bilanciamento: in tal caso si verifica, appunto, un bilanciamento dei valori assunti dalle variabili connesse.
Ovviamente ciò dipende dal tipo di relazioni causali che sussistono tra le variabili interessate e che, nel dettaglio, possono essere:
- relazioni causali positive: una relazione di questo tipo indica che i due nodi o variabili interessate manifestano un cambiamento nella stessa direzione ossia, se il nodo da cui origina il legame diminuisce (aumenta) in valore, anche il valore assunto dall’altro nodo si riduce (aumenta);
- relazioni causali negative: in questo secondo caso, invece, i due nodi o variabili di interesse mutano secondo direzioni opposte ovvero, se il nodo da cui origina il legame aumenta (diminuisce) in valore, allora il valore assunto dall’altro nodo si riduce (cresce).
Costruzione del Diagramma Causale
Definiti gli elementi fondamentali atti a permettere un’efficace realizzazione di un diagramma causale, si riporta di seguito lo specifico Causal Loop Diagram relativo alla metodologia proposta nel presente lavoro.
FIGURA 2
Dalla figura 2 è possibile individuare quattro macro fasi per lo sviluppo della metodologia: una fase preliminare di raccolta e validazione dei dati necessaria per la previsione dei meccanismi di degrado e dei modi di guasto di un componente o di una attrezzatura. Una seconda fase valutazione del livello di rischio associato ad ogni componente ed una conseguente attività di definizione delle priorità di intervento, in termini di ispezioni e manutenzioni. Una terza fase legata alla valutazione economica della strategia ispettiva e manutentiva proposta, con la relativa analisi delle risorse disponibili, sia su scala annuale che mensile, necessaria per l’esecuzione del piano. Infine vi è poi una fase di reportistica consistente nella valutazione degli indicatori prestazionali legati alle attività di manutenzione ed agli effetti di queste ultime sulla produzione. Nel dettaglio si può osservare che, l’incipit è fornito dai dati storici immagazzinati nel sistema informativo industriale. Tali dati non riguardano solo ed esclusivamente gli aspetti legati alla manutenzione ed ispezione, bensì vengono considerati tutta una serie di elementi correlati alla produzione, all’organizzazione del lavoro e dei macchinari ed alle caratteristiche
tecniche di questi ultimi. La peculiarità principale da sottolineare in questa fase riguarda il fatto che, ogniqualvolta viene raccolto un nuovo dato, esso deve essere validato. Il processo di validazione prevede che le informazioni afferenti ad una stessa categoria vengano confrontate, controllandone la compatibilità con limiti fisici e tecnici mediante l’ausilio di standard o linee guida. Il risultato di tale processo sarà una valutazione complessiva di tutti i dati rilevanti per la quantificazione del rischio dei componenti di interesse; definiti “raw data”. I dati grezzi sono utilizzati per effettuare delle previsioni sui meccanismi di degrado dei componenti. Tali previsioni vengono però corrette attraverso il giudizio degli esperti del settore. In questo modo è possibile predire i meccanismi di degrado delle apparecchiature soggette ad usura, grazie alla conoscenza delle distribuzioni teoriche e delle funzioni empiriche correlate ai dati a disposizione.
Tramite i meccanismi di degrado, è possibile conoscere i possibili modi di guasto di un componente o del sistema, che nella realtà non sono meramente di tipo binario. Inoltre, poiché i guasti possono essere anche di natura accidentale, è necessario modellare la casualità di un malfunzionamento attraverso un processo stocastico, ovvero una collezione di variabili aleatorie randomiche, che immettono nel sistema considerato un certo grado di incertezza. Una volta definiti i possibili modi di guasto dell’attrezzature o del sottosistema considerato, si prosegue con la valutazione della probabilità e delle conseguenze di guasto, per poi determinare il livello di rischio. Tale livello risulta indispensabile per definire il grado di priorità delle attività operative RBI e RBM. In particolare, attraverso i controlli non distruttivi e gli esami visivi realizzati durante le ispezioni, si avranno a disposizione dei dati di sopravvivenza più robusti, in termini di affidabilità e vita media residua del componente che, attraverso un loop di rinforzo, consentono di migliorare la stima legata ai possibili modi di guasto del sottosistema considerato. Attraverso le attività operative di RBI ed RBM, è possibile valutare le strategie ispettive e manutentive da applicare alla linea produttiva nel suo complesso. Ovviamente tale valutazione non può prescindere da un’opportuna analisi economica basata sulla valutazione dei costi, non solo diretti ma anche indiretti, ovvero correlati agli errori commessi durante le attività RBI ed RBM, che comportano inevitabilmente delle spese derivanti da un elevato tasso di difettosità degli item prodotti. L’analisi dei costi dovrà inevitabilmente interfacciarsi con il controllo della disponibilità delle risorse, in termini di tempo, manodopera, attrezzature ed extra budget. In base a tale disponibilità, viene realizzato un piano ispettivo/manutentivo su scala annuale che deve poi essere tradotto in piani mensili, prevedendo una nuova analisi delle risorse. Se queste ultime possono essere allocate in maniera bilanciata nei vari intervalli di tempo previsti per le attività operative di manutenzione ed ispezione, si passa all’esecuzione del piano mensile. Per legati alle attività di manutenzione ed all’influenza che queste ultime hanno sulla produzione di item conformi alle specifiche. Dunque, da un lato viene valutata la bontà delle attività manutentive, e dall’altro il tasso di difettosità delle parti prodotte, che se superiore ad un certo valore soglia, comporta elevati costi indiretti legati agli errori di manutenzione. Dalla figura inoltre si evidenzia come la fase di reportistica basata sugli indicatori generali di prestazione delle attività manutentive formi un loop di rinforzo con i dati storici, mentre il tasso di difettosità costituisce un loop dello stesso tipo con i costi di manutenzione imperfetta. In definitiva, nella figura allegata è possibile identificare l’essenza delle relazioni causali che sussistono tra le diverse variabili considerate e che risultano essere tutte delle relazioni causali positive. Inoltre, sono identificati i tre circuiti di
rinforzo che determinano un aggiornamento continuo delle informazioni, secondo gli aspetti precedentemente commentati.
Come già accennato, questo diagramma, estremamente semplice ma altamente informativo, al fine di un futuro lavoro, costituisce il primo passo per una successiva particolarizzazione dei concetti appena esposti all’interno di un software simulativo basato sulla System Dynamics.
Conclusioni
In conclusione, le evidenze ottenute con tale lavoro dimostrano che è possibile adottare una procedura rigorosa per la gestione della manutenzione che consenta di tenere presenti molteplici aspetti di un impianto industriale quali:
- la definizione delle priorità di intervento ispettivo
- manutentivo sulla base del rischio di rottura di un compente critico;
- la valutazione delle performance del processo manutentivo ed i riflessi di queste ultime sul processo produttivo;
- l’impostazione delle eventuali misure mitigative sulla base di dati storici, scenari previsionali e giudizio degli esperti;
- l’aggiornamento continuo del Data Base attraverso l’analisi in “real time” delle condizioni di un componente.
In questo studio si cerca di superare la staticità delle metodologie consolidate, quali RBM e RBI, che risultano ampiamente utilizzate nell’industrie di processo. Questo limite viene superato grazie alla logica della System Dynamic mediante l’analisi e lo sviluppo di un Causal Loop Diagram. E’ in fase di sviluppo un modello che possa coniugare gli aspetti statici della metodologia RBIM, presentati in questo studio, con l’esigenza di un’analisi che possa tener conto dell’importanza della variabile tempo, pur considerando funzioni di tipo affidabilistico il cui controllo nel tempo diventa fondamentale nella riduzione del rischio.
VI edizione Safap 2014 - Simulazione dinamica del processo di manutenzione basato sul rischio - a cura di L. C. Santillo, M. Gallo, M. Di Nardo, L. Monica, M. Madonna, F. Giacobbe (Formato pdf, 285 kB).

I contenuti presenti sul sito PuntoSicuro non possono essere utilizzati al fine di addestrare sistemi di intelligenza artificiale.