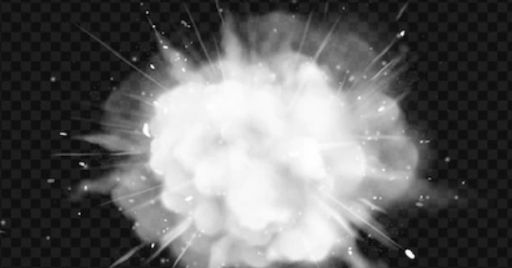
Per utilizzare questa funzionalità di condivisione sui social network è necessario accettare i cookie della categoria 'Marketing'.
Imparare dagli errori: l’esplosione del serbatoio di uno stabilimento
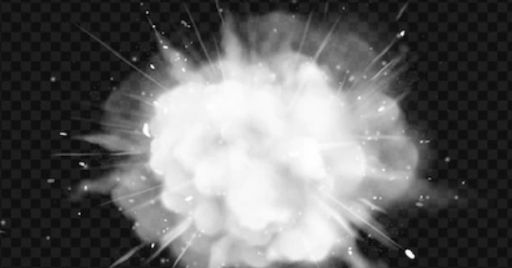
Brescia, 22 Dic – In questi anni i vari convegni SAFAP (Sicurezza ed affidabilità delle attrezzature a pressione) ci hanno permesso di affrontare vari aspetti connessi con i rischi e la prevenzione in relazione alle attrezzature a pressione.
In questi incontri, oltre a presentare nuove ricerche e studi, sono riportate indicazioni sulle buone prassi e sui casi di infortunio che possono essere utili per il miglioramento delle strategie di prevenzione e della sicurezza degli operatori. E questo anche con riferimento ad ambiti lavorativi particolari, come i cosiddetti spazi confinati, in cui possono essere necessari interventi ispettivi, di verifica o di manutenzione delle attrezzature a pressione.
Con riferimento agli atti del convegno SAFAP che si è tenuto nel 2018 - “ SAFAP 2018 - Sicurezza e affidabilità delle attrezzature a pressione. La gestione del rischio dalla costruzione all’esercizio a 130 anni dal primo decreto sulla sicurezza delle caldaie a vapore” (Bologna, 28 e 29 novembre 2018) – ci soffermiamo oggi su un incidente raccontato nell’intervento “Analisi delle criticità gestionali all’origine di incidenti rilevanti recentemente occorsi in Italia – casi di sovrapressione in ambienti totalmente confinati”, a cura di F. Delli Quadri (ISPRA - Servizio per i Rischi e la Sostenibilità Ambientale delle Tecnologie, delle Sostanze Chimiche, dei Cicli Produttivi e dei Servizi Idrici e per le Attività Ispettive).
In questo intervento si affrontano alcuni casi incidentali – oggi ne presentiamo uno – accomunati dalla “dinamica di esplosione da sovrapressione da innesco di miscela infiammabile sviluppatasi all’interno di serbatoi/containers”. Casi incidentali la cui criticità, come raccontato dal relatore, risiede “principalmente nel fatto che, a fronte della semplicità impiantistica del processo e delle apparecchiature coinvolte, gli stessi eventi non sono mai stati ipotizzati nell’analisi di sicurezza, e pertanto neanche gestiti a livello di adozione delle necessarie misure preventive e mitigative, tecniche e gestionali”.
Questi gli argomenti trattati nell’articolo:
- L’esplosione di un serbatoio e la dinamica dell’incidente
- L’analisi delle cause e delle criticità gestionali all’origine dell’incidente
L’esplosione di un serbatoio e la dinamica dell’incidente
Il caso, su cui ci soffermiamo, riguarda l’esplosione di un serbatoio atmosferico di equalizzazione in uno stabilimento farmaceutico.
L’incidente, racconta il relatore, si è verificato in uno stabilimento dedicato alla fabbricazione di prodotti farmaceutici di base mediante procedimento chimico-biologico e l’apparecchiatura origine dell’evento “è un serbatoio equalizzatore TK ubicato nella sezione trattamento reflui provenienti dal recupero solventi dell’impianto per la produzione di Rifamicina O”. Il serbatoio ha “la funzione di polmone di stoccaggio e di equalizzazione del “brodo esausto strippato” (BES), ovvero del refluo derivante dalla produzione di antibiotico rifamicina, e proveniente direttamente dal reparto di estrazione della rifamicina”.
Rimandiamo alla lettura integrale dell’intervento che descrive il serbatoio di equalizzazione TK e ci soffermiamo sulla dinamica dell’incidente.
Si indica che nel corso di un intervento di una modifica programmata sulla linea di alimentazione al serbatoio TK, “durante lavori di tipo ‘a caldo’ sul serbatoio si è verificata una esplosione confinata del serbatoio, con proiezione del tetto a distanza di circa 20 m: l’esplosione ha determinato la morte di un operatore esterno ed il ferimento di 4 altri operatori (3 esterni + 1 interno), tutti impegnati nell’intervento di modifica. Scopo dell’intervento era quello di modificare la linea di alimentazione del BES nel TK con inserimento di uno stacco per il collegamento di una tubazione proveniente dal reparto fermentazione al fine di convogliare, nello stesso serbatoio TK, il refluo BES derivante dalla prova sperimentale di fermentazione effettuata per la nuova produzione di antibiotico Spiramicina”.
Si indica che la linea d’alimentazione BES “era stata svuotata dal refluo proveniente dal reparto distilleria. Lo sfiato del serbatoio collocato sulla sommità del tetto era aperto come di sua natura. Il serbatoio era pieno per circa 50% del suo volume. 5 operatori erano impegnati nell’esecuzione del lavoro, 4 dipendenti da ditta esterna e uno interno. Gli operatori della ditta esterna avevano scollegato la linea di alimentazione BES rimuovendo la valvola di intercettazione sul bocchello di ingresso posto sul tetto del serbatoio TK, senza previa chiusura con flangia cieca del bocchello. Un operatore era posizionato sul tetto del TK in prossimità della flangia del bocchello aperto; gli altri operatori si trovavano sulla passerella di accesso al tetto del serbatoio. Stavano quindi iniziando a tagliare il tubo esistente con una mola circolare; probabilmente al contatto della mola elettrica con la tubazione, le scintille prodotte hanno provocato l’innesco di atmosfera esplosiva, non prevista ma presente all’interno del serbatoio”.
L’analisi delle cause e delle criticità gestionali all’origine dell’incidente
Veniamo alle cause dell’incidente.
Vengono presentate prima le cause dirette, sulla base delle informazioni raccolte in fase di successivo sopralluogo e dei risultati dell’indagine giudiziaria condotta sull’esplosione, “ipotizzate e considerate plausibili:
- nel serbatoio era presente una miscela esplosiva di gas/vapori, innescata dal taglio della tubazione eseguito con uso di una mola elettrica;
- tale miscela di gas/vapori infiammabili è stata prodotta da una fermentazione anaerobica del BES presente nel serbatoio TK, avvenuta attraverso diversi tipi di batteri non facilmente identificabili (poiché dopo l’esplosione il BES è venuto a contatto con l’aria a seguito dell’asportazione del tetto del serbatoio);
- tale fermentazione anaerobica è stata resa possibile dall’accumulo e permanenza nel tempo di fanghi e reflui pesanti su fondo e pareti del serbatoio, a causa di assenza di idoneo sistema di miscelazione. Le analisi eseguite sul refluo BES (fase liquida e solida) confermerebbero la formazione, a seguito della fermentazione anaerobica, di idrogeno, metano, solfuro di carbonio, tiometano, carbonil solfuro e altri gas solforati infiammabili, che dunque sarebbero fra i componenti della miscela gas/vapori esplosiva presente all’interno del serbatoio TK”. La fase solida “formata per sedimentazione dei componenti organici e inorganici più pesanti del BES (residui), tra cui micelio morto, ha funzionato da matrice base di proliferazione di batteri anaerobici non previsti, che hanno trasformato biochimicamente il residuo organico del BES (concentrato del liquido), in presenza di ioni zolfo derivanti dai persolfati, in composti volatili infiammabili (componenti della miscela infiammabile). La fermentazione è probabilmente avvenuta attraverso diversi tipi di batteri non facilmente identificabili in quanto dopo l’esplosione il liquido (refluo) presente nel serbatoio è venuto a contatto con l’aria a seguito dell’asportazione del tetto del serbatoio stesso”.
Veniamo poi alle cause indirette o di radice e alle carenze gestionali SGS connesse.
In corrispondenza alle cause dirette ipotizzabili vengono dunque estrapolate “cause ‘di radice’, legate agli aspetti gestionali del Sistema di Gestione della Sicurezza ex d.lgs.105/15 e all’applicazione della normativa sulla Sicurezza sul Lavoro ex d.lgs. 81/08 e s.m.i. che, sulla base delle informazioni raccolte hanno avuto un ruolo nel verificarsi dell’evento stesso e nella sua evoluzione”.
In particolare per quanto attiene la Direttiva ATEX (ultima versione ATEX 2014/34/UE) “esiste l’obbligo per il datore di lavoro della valutazione dei rischi di formazione di atmosfere esplosive, con individuazione attraverso adeguata analisi delle aree a diverso livello di rischio. In funzione del livello di rischio, inoltre, vanno utilizzate attrezzature marchiate ATEX ed adottate altre misure preventive incluse segnaletica e formazione del personale”. E l’azienda “aveva in generale ottemperato alla normativa, affidandosi ad una ditta di consulenza specialistica: tuttavia l’area trattamento acque reflue provenienti da produzione di rifamicina non era stata considerata a rischio di esplosione. Pertanto l’applicazione della normativa, pur se eseguita, non si è rivelata adeguata per via di tale errore che certamente si poteva evitare: la formazione di biogas da fermentazione di reflui organici, seppure in settori diversi, è un fenomeno comunque noto, anche se poco probabile. Sarebbe stato dunque più corretto classificare l’area di interesse come zona 3, cioè ‘Area in cui durante le normali attività non è probabile la formazione di un'atmosfera esplosiva’, per la quale le misure richieste dalla classificazione ATEX sarebbero probabilmente state sufficienti ad evitare l’evento”.
Sono riportati poi altri elementi coinvolti, evidenziati anche in fase di ispezione SGS condotta nello stabilimento:
- Identificazione e valutazione dei pericoli rilevanti ed analisi di rischio: “inadeguati identificazione e aggiornamento della pericolosità connessa con il BES e con il relativo processo di trattamento eseguito. In particolare non era prevista la caratterizzazione del BES all’ingresso del serbatoio (assenza di rapporti di prova di analisi chimiche del BES in ingresso al TK, oltre che in uscita, in modo da poter raffrontare la composizione del BES a monte e a valle del serbatoio). Non è stato valutato il rischio esplosione e non è stata presa in considerazione la possibilità che si potesse formare una atmosfera esplosiva all’interno del TK per fermentazione anaerobica della Biomassa presente nel BES. Nell’analisi di rischio condotta sull’impianto era emersa non critica l’unità di trattamento acque reflue della produzione di rifamicina O, in particolare del processo di equalizzazione all’interno del serbatoio TK, e dunque non era stata effettuata l’analisi di dettaglio (es. con Hazop) che avrebbe certamente rilevato alcune possibili ipotesi incidentali”.
- Adeguamenti impiantistici per la riduzione del rischio: “le condizioni di esercizio del serbatoio TK non erano conformi a quelle specificate sul manuale operativo da progetto, poiché non era attivo il sistema di insufflaggio aria interno che aveva duplice importante funzione:
- garantire la presenza sufficiente di ossigeno in fase liquida per evitare lo sviluppo di attività biologiche anaerobiche con produzione di biogas esplosivo;
- garantire una corretta e completa miscelazione del BES liquido all’interno del serbatoio, realizzata all’epoca solo tramite elica laterale di dimensioni evidentemente ridotte rispetto al diametro del serbatoio, evitando l’accumulo dei fanghi organici nel fondo e sulle pareti del serbatoio. Tale accumulo si è prodotto nell’arco degli ultimi 2 anni”.
- Controllo operativo e procedure di manutenzione: “l’innesco della miscela esplosiva è stato causato dalla inosservanza della procedura sui permessi di lavoro aziendale che prevedeva, nel caso di ‘lavori a caldo’ in situ, le seguenti azioni preventive di sicurezza” (la “mera applicazione della procedura sul p.d.l. aziendale, pur in assenza di adeguata analisi di rischio, avrebbe potuto evitare l’evento incidentale”):
- valutazione, prima della emissione del p.d.l a caldo, della eventualità che il lavoro possa essere effettuato senza l’uso di fiamme libere, ed esame della possibilità di rimozione e trasporto dell’apparecchiatura in un’area non pericolosa;
- preventiva bonifica dell’apparecchiatura;
- ventilazione dei recipienti;
- controlli esplosimetrici delle aree confinate per individuazione presenza gas infiammabili;
- isolamento meccanico della apparecchiatura”.
- Addestramento/formazione del personale: “la mancata applicazione della procedura sui p.d.l. non è solo connessa ad un fattore umano di inattenzione degli operatori che eseguivano il lavoro e che quindi non hanno seguito le misure di sicurezza preventive indicate nella procedura stessa, ma anche ad una carenza di formazione degli stessi operatori, riscontrata in campo dal componente VVF che ha seguito le operazioni di soccorso durante intervista. Inoltre nella procedura p.d.l. viene chiaramente esplicitato che ‘qualunque sistema di isolamento deve essere sempre approvato dal Supervisore del processo interessato’, e pertanto il mancato isolamento era stato evidentemente approvato dal supervisore, come si vede nel modulo p.d.l. compilato, dunque emerge anche una carente formazione del supervisore. Infine la superficialità con cui sono stati compilati e gestiti i moduli dei permessi di lavoro costituisce un ulteriore indicatore della carente formazione e cultura della sicurezza del personale interno ed esterno coinvolto nell’evento”.
- Gestione delle modifiche: “l’intervento oggetto dei lavori era da considerarsi come una modifica impiantistica anche se temporanea (non era la soluzione definitiva) e pertanto oggetto di una adeguata valutazione dei rischi e pianificazione degli interventi. Una HSE review era stata effettuata il giorno prima della modifica ma non sono stati valutati i rischi possibili connessi con la modifica. Anche per l’intervento di modifica conseguente al revamping effettuato in passato, di ciecatura del sistema di insufflaggio aria interno al serbatoio, non era stata stata effettuata analisi di rischio. In entrambi i casi una preventiva e adeguata analisi del rischio avrebbe potuto evitare l’incidente”.
Rimandiamo ad una lettura integrale dell’intervento che riporta non solo ulteriori indicazioni e riflessioni sulle criticità gestionali emerse, ma anche immagini e disegni esplicativi degli incidenti presentati.
Tiziano Menduto
Scarica il documento da cui è tratto l'articolo:
Inail, Dipartimento innovazioni tecnologiche e sicurezza degli impianti, prodotti e insediamenti antropici, “ SAFAP 2018 - Sicurezza e affidabilità delle attrezzature a pressione. La gestione del rischio dalla costruzione all’esercizio a 130 anni dal primo decreto sulla sicurezza delle caldaie a vapore”, atti del convegno SAFAP 2018 a cura di Francesca Ceruti e Daniela Gaetana Cogliani, edizione 2018 (formato PDF, 29.42 MB).
Vai all’area riservata agli abbonati dedicata a “ La sicurezza e l’affidabilità delle attrezzature a pressione”.

I contenuti presenti sul sito PuntoSicuro non possono essere utilizzati al fine di addestrare sistemi di intelligenza artificiale.
Per visualizzare questo banner informativo è necessario accettare i cookie della categoria 'Marketing'