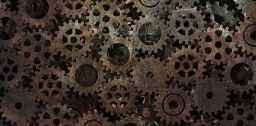
Industria: come affrontare i rischi di invecchiamento degli impianti?
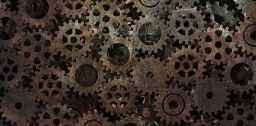
Bologna, 7 Giu – Nel panorama industriale si possono riscontrare sia realtà produttive con impianti all’avanguardia, sia realtà con impianti “la cui età ha già sorpassato la vita utile ipotizzata in fase di progetto”, ma che, per diversi motivi, “non sono stati sostituiti con alternative più moderne”.
Se in questi ultimi casi gli impianti “iniziano a manifestare gli effetti dell’usura” e ad avere problemi di produttività e di sicurezza, “una delle vie per gestire gli impianti che stanno invecchiando è un’oculata manutenzione”.
A ricordacelo e a fornire una metodologia per la pianificazione della manutenzione di tipo proattivo è un intervento al convegno SAFAP 2018 (Bologna, 28 e 29 novembre 2018), intervento contenuto nella pubblicazione Inail “ SAFAP 2018 - Sicurezza e affidabilità delle attrezzature a pressione. La gestione del rischio dalla costruzione all’esercizio a 130 anni dal primo decreto sulla sicurezza delle caldaie a vapore” che raccoglie gli atti del convegno.
Ci soffermiamo, in particolare, sui seguenti argomenti:
- I rischi dell’invecchiamento degli impianti
- Analisi decisionale dinamica integrata
- Esempi applicativi e sviluppi della metodologia
I rischi dell’invecchiamento degli impianti
L’intervento “Ottimizzazione delle strategie manutentive delle apparecchiature datate mediante l’applicazione dell’analisi decisionale dinamica integrata”, a cura di M. Demichela e G. Baldissone (Politecnico di Torino), C. Leva (Dublin Institute of Technology) e P. Agnello (Inail – Dit), si sottolinea che “l'invecchiamento degli impianti, se gestito in modo non corretto, può causare gravi incidenti”.
In particolare l'Health and Safety Executive (UK) ha identificato, tra il 1980 e il 2006, nella banca dati MARS (Major Accident Reporting System) “96 incidenti legati all'invecchiamento d’impianti e attrezzature, corrispondenti al 23% dei principali incidenti verificatisi nello stesso periodo”. E questi incidenti hanno comportato “costi elevati sia in termini economici (oltre 170.000.000 €) che in termini di vittime (11 morti, 183 feriti) e di impatti ambientali”.
Inoltre l’utilizzo di attrezzature oltre il loro periodo di vita utile “riduce la competitività dell'azienda, poiché di solito queste richiedono più energia, più manutenzione e materie prime, spesso, costose”. Invece l'adozione di impianti moderni e con una maggiore attenzione alla sostenibilità, “possono utilizzare meno energia, e possono aumentare la flessibilità dell'impianto sia per quanto riguarda i volumi prodotti che per la tipologia di prodotti ottenuti”. Senza dimenticare che l’uso di impianti moderni o datati ha un evidente impatto anche sulla sicurezza di processo e degli operatori: “il guasto di un’attrezzatura o impianto può essere un precursore o una causa diretta di infortuni, incidenti e impatti ambientali”.
Il problema è che l'adozione di nuove tecnologie e il rinnovo degli impianti “richiedono elevati costi di investimento, il che porta insieme ad altri vincoli, ad utilizzare gli impianti oltre la loro vita utile nonostante le potenziali criticità”.
Tuttavia per minimizzare le criticità degli impianti datati è necessario “gestire l’invecchiamento degli impianti e attrezzature anche attraverso la manutenzione”.
Si sottolinea poi che se generalmente la strategia di manutenzione “è scelta tra la manutenzione reattiva e la manutenzione preventiva”, lo sviluppo tecnologico “consente ora di sviluppare strategie manutentive basate sulle reali condizioni delle apparecchiature, con un approccio proattivo”.
L’intervento, nell’ambito del progetto Saf€ra PROAGE, finanziato da Inail, si propone una metodologia per la pianificazione della manutenzione di tipo proattivo e basato sulla stima dei valori di rischio.
In particolare viene proposto e discusso un approccio “basato su dati di rischio al fine di operare una scelta tra diverse strategie manutentive concorrenti. La metodologia discussa analizza il rischio associato alle diverse strategie manutentive in base alle possibili condizioni dell'apparecchiatura al momento di inizio delle attività di manutenzione”.
La valutazione del rischio è effettuata tramite “l’Integrated Dynamic Decision Analysis (IDDA)”.
Analisi decisionale dinamica integrata
relatori indicano che l’Integrated Dynamic Decision Analysis (IDDA), sviluppato da Remo Galvagni, “è stato applicato a diversi casi studio al fine di supportare processi decisionali basati sui dati di rischio”.
In particolare la metodologia IDDA accoppia un modello logico-probabilistico e un modello fenomenologico. Riprendiamo dal documento una rappresentazione grafica dell’integrazione fra modello logico – probabilistico e modello logico:
In particolare la modellazione logico-probabilistica procede attraverso i seguenti passaggi:
- L'analisi funzionale del sistema e la costruzione di un elenco di livelli, attraverso una serie di domande e affermazioni sulla funzionalità di ciascun elemento; ogni livello rappresenta l’elemento base del modello logico, il quale in un albero degli eventi corrisponderebbe a un nodo.
- La costruzione di una struttura reticolare attraverso gli indirizzamenti (livelli successivi) di uscita in ogni livello.
- Caratterizzazione di ogni livello e ogni possibile alternativa di uscita dei livelli con una stringa di testo che consente all'utente di leggere lo sviluppo logico di ogni sequenza di eventi;
- L'associazione a ciascun livello di un dato probabilistico, che rappresenta il grado previsto di probabilità di occorrenza di ogni evento analizzato e di un dato d’incertezza della probabilità di accadimento, che rappresenta la distribuzione statistica della probabilità.
- La definizione di vincoli logici e probabilistici, che consentono di tenere in considerazione le interdipendenze esistenti fra i vari eventi analizzati.
E assieme al modello logico – probabilistico viene preparato un modello fenomenologico che “descrive il comportamento fisico del sistema. Il modello fenomenologico può partecipare all’aggiornamento delle risultanze del modello logico – probabilistico al fine di avvicinare i risultati dell’analisi alla realtà, cioè, ad esempio, se dopo il guasto di un’apparecchiatura le altre apparecchiature sono in grado di compensare il guasto, o se possono comparire effetti cumulativi e divergenti portando ad eventi potenzialmente pericolosi”.
Inoltre il modello fenomenologico “può fornire anche una stima delle conseguenze per ogni singola sequenza di eventi individuata in moda da ottenere una stima del rischio, la valutazione del rischio complessivo del sistema e il valore atteso delle conseguenze”.
Esempi applicativi e sviluppi della metodologia
Nell’intervento questa metodologia descritta è stata poi testata “per confrontare diverse strategie per la manutenzione di una turbina in un impianto turbogas, tenendo conto dei fenomeni legati all’invecchiamento”.
Ed è stato così possibile discriminare tra le diverse soluzioni di manutenzione alternative:
- Opzione 1: apertura della turbina per l’ispezione e la manutenzione, senza palette di ricambio stoccate;
- Opzione 2: apertura della turbina per l’ispezione e la manutenzione, avendo immagazzinato uno stock di palette (in base all’esperienza aziendale, di prassi sono stoccate 7 palette);
- Opzione 3: eseguire la manutenzione sostituendo l’intero set delle palette;
- Opzione 4: sostituire l’intero set di palette (sia del rotore che del distributore) con palette di nuova generazione più efficienti;
Rimandiamo alla lettura integrale dell’intervento che mostra come sia stato possibile ottimizzare la manutenzione di una turbina a gas, nell’ottica di valutare gli effetti potenziali di un ritardo nella manutenzione legato alla disponibilità di parti di ricambio.
L’intervento si conclude ricordando che in diversi stabilimenti industriali “l'invecchiamento dell'apparecchiatura sta diventando un problema pressante” e può “causare incidenti, aumentare il dispendio energetico e generare costi aggiuntivi”.
Se uno dei modi per controllare l'invecchiamento delle attrezzature è una corretta manutenzione, è possibile utilizzare un approccio “per valutare i pro e i contro di diverse strategie manutentive attraverso la stima dei dati di rischio delle diverse scelte proposte”. E i futuri sviluppi dell’approccio proposto permetteranno poi di tenere in considerazione sempre più anche gli aspetti legati al potenziale rischio di incidente.
RTM
Scarica il documento da cui è tratto l'articolo:
Inail, Dipartimento innovazioni tecnologiche e sicurezza degli impianti, prodotti e insediamenti antropici, “ SAFAP 2018 - Sicurezza e affidabilità delle attrezzature a pressione. La gestione del rischio dalla costruzione all’esercizio a 130 anni dal primo decreto sulla sicurezza delle caldaie a vapore”, atti del convegno SAFAP 2018 a cura di Francesca Ceruti e Daniela Gaetana Cogliani, edizione 2018 (formato PDF, 29.42 MB).
Vai all’area riservata agli abbonati dedicata a “ La sicurezza e l’affidabilità delle attrezzature a pressione”.

I contenuti presenti sul sito PuntoSicuro non possono essere utilizzati al fine di addestrare sistemi di intelligenza artificiale.