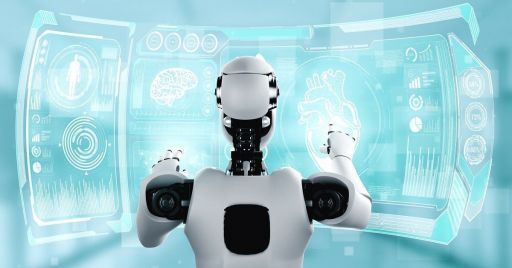
Per utilizzare questa funzionalità di condivisione sui social network è necessario accettare i cookie della categoria 'Marketing'.
Imparare dagli errori: i rischi della manutenzione nelle attività automatizzate
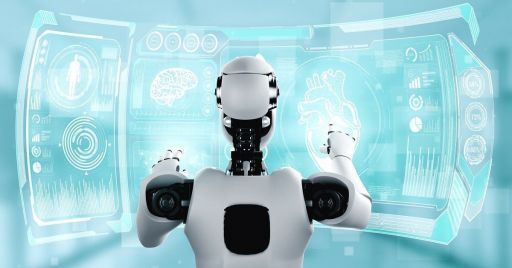
Brescia, 6 Feb – Abbiamo iniziato nelle scorse settimane, anche con riferimento alla campagna europea “ Lavoro sano e sicuro nell’era digitale”, di cui PuntoSicuro è mediapartner, un breve viaggio intorno agli infortuni, gravi o mortali, che possono avvenire in ambiti lavorativi in cui siano presenti sistemi robotici e sistemi di automazione.
Sistemi che, insieme a varie attrezzature tecnologicamente avanzate possono migliorare la prevenzione, riducendo o anche eliminando alcuni rischi (ad esempio evitando compiti noiosi e ripetitivi, lavori ad alto rischio o riducendo il rischio da sovraccarico biomeccanico), ma che possono anche introdurre nuovi pericoli per il lavoratore.
Pericoli che poi aumentano durante le attività di manutenzione, svolte sui sistemi di automazione o in presenza di questi, quando non sono rispettate, come vedremo oggi, idonee precauzioni e procedure lavorative o sono assenti adeguati dispositivi di protezione.
Anche in questa puntata della rubrica “ Imparare dagli errori”, dedicata al racconto degli infortuni professionali, le dinamiche infortunistiche presentate sono tratte dalle schede dell’archivio di INFOR.MO., strumento per l'analisi qualitativa dei casi di infortunio collegato al sistema di sorveglianza degli infortuni mortali e gravi.
Questi gli argomenti trattati nell’articolo:
- Esempi di infortuni nella manutenzione di sistemi robotici
- Uomini, robot e sistemi di automazione: rischi e prevenzione
Esempi di infortuni nella manutenzione di sistemi robotici
Nel primo caso l’infortunio avviene a un manutentore in una fonderia.
Un manutentore entra nell'area operativa di un "robot sollevatore di lingotti" di una fonderia, entrandovi da un accesso non segregato o protetto.
L'operazione che sta svolgendo è di ingrassaggio dei cuscinetti del nastro trasportatore dei lingotti, provenienti da un altro nastro trasportatore del forno.
Non avendo fermato l'impianto ed oscurando inavvertitamente le fotocellule di processo, il robot continua a svolgere il ciclo di lavoro abituale e nel suo percorso schiaccia la testa dell'operatore con le ganasce di presa e sollevamento del pacco di lingotti, provocandone il decesso.
Questi i fattori causali rilevati:
- “area operativa della macchina priva di accesso protetto”;
- “il manutentore entrava nell'area operativa del robot entrandovi da un accesso non segregato o protetto e non fermava l'impianto, oscurando inavvertitamente le fotocellule di processo”.
Nel secondo caso l’infortunio avviene in un’azienda di piccole dimensioni di produzione di carta, cartoni e prodotti affini dove, sulla linea automatica per la scatolatura di pacchetti di salviette asciugamani in carta piegati a Z, erano in corso lavori di cambio di ciclo.
La linea era stata fermata fin dalla mattina. Era costituita da un robot antropomorfo e da un apparato di formatura e chiusura scatole, il primo comandato dalla propria unità di governo (terminale remoto o tastierino), il secondo gestito da PLC (Programmable Logic Controller - controllore logico programmabile).
La scheda di Informo indica che “le zone di lavoro dell’operatore durante la marcia della macchina sono sostanzialmente due: quella esterna alla macchina e la zona A di carico scatole accessibile per rifornire la linea delle scatole da un cancello dotato di elettroserratura comandata dalla pulsantiera esterna. Vi è anche una zona B o area robotizzata accessibile dalla zona A mediante un altro cancello dotato anch’esso di elettroserratura che se azionata blocca il ciclo di lavoro”.
Un lavoratore dopo aver effettuato pulizie della zona di lavoro e aver rifornito di materiale la macchina, “aveva aiutato un manutentore esperto in alcune lavorazioni meccaniche. Aveva quindi avvertito il manutentore che avrebbe atteso l’altro manutentore per il cambio elettronico del programma di lavoro da effettuare dal pannello di comando della scotolatrice”.
Poco dopo il lavoratore viene trovato nella zona B con il corpo schiacciato tra la struttura della scotolatrice e la pinza del robot; il decesso è stato immediato. “In tale zona è stato ritrovato anche il tastierino di comando del robot. E’ verosimile che il lavoratore si sia impegnato da solo nelle operazioni di regolazione fornendo energia alla linea, e, verificando che la pinza del robot non lavorava bene, prima abbia provato ad agire dalla zona A e successivamente abbia sorpassato le barriere fisse che separano la zona A da quella B (il passaggio è disagevole ma possibile attraverso un varco di 90 x 105 cm) trascinandosi il tastierino di azionamento del robot. In quella posizione avrebbe sollecitato un sensore che ha comandato l’azione della pinza”.
Questo il fattore causale riportato nella scheda:
- “il lavoratore si insinua sotto le barriere fisse ed aziona la pinza del robot da una posizione pericolosa”.
Uomini, robot e sistemi di automazione: rischi e prevenzione
Per raccogliere qualche spunto informativo generale sui rischi in presenza di sistemi robotici e di automazione, torniamo a soffermarci sul contenuto di un contributo – e a cura di Adel Sghaïer (INRS) e Liên Wioland (INRS) - presente nel dossier francese INRS e dal titolo "Hommes — robots : collaborer en sécurité” (dossier pubblicato nella rivista tecnica dell’INRS “Hygiène & sécurité du travail” n° 268).
Il contributo, dal titolo “Robotique collaborative: les enjeux en prevention des risques professionnels”, riprende alcune indicazioni sui rischi associati alla collaborazione uomo e robot, almeno nel caso particolare dell’utilizzo di robot collaborativi ( cobot).
Ad esempio ci sono i rischi legati alla macchina. Si indica che anche se nei robot collaborativi la velocità dei movimenti e l'energia trasmessa in caso di collisione sono inferiori a quelle di un robot convenzionale, il rischio meccanico rimane il fattore di rischio predominante nella maggior parte delle applicazioni robotiche, siano esse collaborative o meno. Un fenomeno che comporta, tra l'altro, rischi di schiacciamento, intrappolamento o impatto. E anche se meno significativi, occorre poi tenere conto anche di altri rischi "macchina", come il rumore, i rischi termici o elettrici. Infine, occorre prestare particolare attenzione ai rischi associati agli strumenti utilizzati dal robot per svolgere il proprio compito e, più in generale, ai rischi associati ai processi.
Il documento si sofferma poi anche sui rischi psicosociali, sui disturbi muscoloscheletrici e su come l'attività degli operatori cambierà cambiando con l’uso di robot collaborativi.
Si presentano poi alcune misure/soluzioni tecniche:
- arresto del robot ("arresto di sicurezza nominale controllato"): consiste nell'arrestare il robot quando l'operatore entra nell'area di lavoro condivisa dal robot e dall'operatore (area di lavoro collaborativa), per evitare qualsiasi rischio di collisione. Il robot può poi riprendere il lavoro in modalità automatica non appena l'operatore lascia l'area di lavoro. La maggior parte dei produttori di robot offre schede o moduli di sicurezza che consentono di implementare questo tipo di collaborazione, grazie ad apposite funzioni di sicurezza;
- guida manuale: viene utilizzata quando l'operatore è a diretto contatto con il robot. Le azioni dell'utente (sforzo, movimento) vengono misurate e utilizzate per muovere il robot. Questo tipo di interazione può essere utilizzato sia per le fasi di apprendimento e impostazione che per le fasi di produzione;
- distanza tra operatore e robot ("controllo della velocità e della distanza di separazione"): garantisce che il robot si muova a velocità ridotta, mantenendo una distanza definita dall'operatore. L'obiettivo è prevenire le collisioni, senza fermare il robot quando possibile. Tuttavia, se la distanza di separazione non viene più mantenuta, viene attivato un arresto di sicurezza. Uno degli elementi chiave di questa sicurezza è l'uso di dispositivi in grado di riconoscere l'operatore e di rilevarne i movimenti in tempo reale. Per svolgere questo compito sono state sviluppate alcune tecnologie basate su telecamere o sensori capacitivi;
- arresto durante il contatto uomo-robot ("limitazione della potenza e della forza del robot"): implica l'implementazione di dispositivi in fase di progettazione del robot e/o nel sistema di controllo per limitare le forze di contatto in caso di collisione con l'operatore. Il robot deve essere in grado di rilevare il superamento delle soglie di forza e potenza definite nel documento tecnico ISO TS 15066 in caso di contatto con un operatore e di arrestare il proprio movimento in modo sicuro.
Rimandando alla lettura integrale del documento che si sofferma anche sulle possibili misure collettive e organizzative, ricordiamo poi che, con riferimento ai casi presentati oggi, il nostro giornale ha pubblicato negli anni numerosi articoli dedicati alle attività di manutenzione in sicurezza.
Ad esempio nell’articolo di presentazione del “ Factsheet n. 88: Manutenzione sicura — Lavoratori sicuri” sono presentate cinque regole di base per rendere più sicura la manutenzione:
- pianificazione
- messa in sicurezza dell'area di lavoro
- uso di attrezzature adeguate
- lavoro svolto secondo quanto pianificato
- verifica finale
Si indica poi che è necessario “seguire le prassi di lavoro sicuro sviluppate in fase di pianificazione”. Ed è, dunque, importante pianificare le attività di manutenzione e il piano di lavoro “deve essere seguito anche quando il tempo è scarso: le procedure abbreviate possono essere molto costose e possono produrre incidenti, infortuni o danni ai beni”. E “potrebbe essere necessario avvisare i supervisori e/o consultare altri esperti nel caso in cui si verificasse qualche evento imprevisto. È molto importante ricordare anche che oltrepassare l’ambito delle proprie abilità e competenze potrebbe causare un incidente molto grave”.
Ricordiamo, in conclusione, alcune puntate della rubrica “Imparare dagli errori” sul tema della manutenzione:
- Imparare dagli errori: gli infortuni nella manutenzione delle macchine
- Imparare dagli errori: ancora sulle cattive prassi nella manutenzione
- Imparare dagli errori: la manutenzione in mancanza di idonee procedure
Tiziano Menduto
Sito web di INFOR.MO.: nell’articolo abbiamo presentato le schede di Infor.mo. 11709 e 16011 (archivio incidenti 2002/2021).
Scarica le schede da cui è tratto l'articolo:

I contenuti presenti sul sito PuntoSicuro non possono essere utilizzati al fine di addestrare sistemi di intelligenza artificiale.
Per visualizzare questo banner informativo è necessario accettare i cookie della categoria 'Marketing'