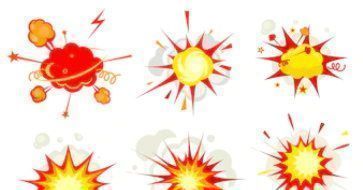
Per utilizzare questa funzionalità di condivisione sui social network è necessario accettare i cookie della categoria 'Marketing'.
Imparare dagli errori: i rischi di sovrapressione e le sostanze pericolose
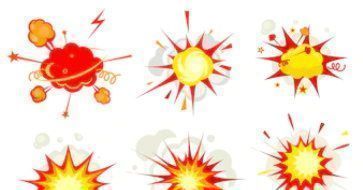
Brescia, 18 Gen – Come ricordato nei nostri articoli, l’analisi degli incidenti industriali, specialmente nelle attività a rischio rilevante , può costituire una fonte basilare da cui ricevere utili lezioni tecniche e gestionali; lezioni che possono essere utili sia ai gestori e gli operatori delle industrie a rischio di incidente rilevante, sia alle pubbliche Amministrazioni impegnate nelle attività di controllo.
L’analisi di questi eventi “costituisce da sempre un’attività fondamentale nell’ambito delle funzioni di prevenzione e controllo del rischio nelle aree industriali svolte dal Settore VAL-RTEC-IND di Ispra, sia per ottenere e monitorare una visione panoramica della situazione incidentale a livello nazionale, sia per focalizzare l’attenzione su specifici aspetti di interesse relativi alle diverse tipologie di rischio presenti nelle realtà industriali Seveso, dove la presenza di sostanze pericolose risulta determinante come fattore aggravante nella possibilità di accadimento/evoluzione di incidente”.
A ricordarlo è l’intervento “Analisi delle criticità gestionali all’origine di incidenti rilevanti recentemente occorsi in Italia – casi di sovrapressione in ambienti totalmente confinati”, a cura di F. Delli Quadri (ISPRA - Servizio per i Rischi e la Sostenibilità Ambientale delle Tecnologie, delle Sostanze Chimiche, dei Cicli Produttivi e dei Servizi Idrici e per le Attività Ispettive), presentato al convegno “ SAFAP 2018 - Sicurezza e affidabilità delle attrezzature a pressione. La gestione del rischio dalla costruzione all’esercizio a 130 anni dal primo decreto sulla sicurezza delle caldaie a vapore” (Bologna, 28 e 29 novembre 2018).
L’intervento sofferma l’attenzione, “nell’ambito della tematica del rischio pressione associato a presenza di sostanza pericolosa, sullo specifico aspetto rischio di sovrapressione in ambienti totalmente confinati (apparecchiature, sistemi) inclusi quelli funzionanti a pressione atmosferica”.
Il lavoro approfondisce 2 casi incidentali rilevanti mortali “occorsi negli ultimi anni in stabilimenti soggetti al d.lgs. 105/15 ubicati in territorio nazionale, accomunati dalla dinamica di esplosione da sovrapressione da innesco di miscela infiammabile sviluppatasi all’interno di serbatoi/containers”. E si indica che la ricerca delle cause di radice e carenze gestionali a monte della sovrapressione diventa “fondamentale per comprendere e prevenire tali tipologie di incidenti che, in sistemi semplici con condizioni di esercizio sostanzialmente non critiche, non risultano normalmente ipotizzati nell’analisi di rischio”.
Se in una precedente puntata di “ Imparare dagli errori”, rubrica dedicata al racconto degli infortuni professionali, ci siamo soffermati sull’esplosione di un serbatoio atmosferico in uno stabilimento farmaceutico, oggi affrontiamo il caso dell’esplosione di un fusto metallico.
Questi gli argomenti trattati nell’articolo:
- L’esplosione di un fusto metallico e la dinamica dell’incidente
- L’analisi delle cause e delle criticità gestionali all’origine dell’incidente
L’esplosione di un fusto metallico e la dinamica dell’incidente
L’incidente, su cui ci soffermiamo, si è verificato in uno stabilimento dove si svolge “attività di tipo commercio all’ingrosso e distribuzione di prodotti chimici e petrolchimici, quali acetati, solventi e diluenti e formulazione di miscele di solventi”.
Una volta in stabilimento, i prodotti “sono scaricati e stoccati in serbatoi interrati, nei quali vengono trasferiti dalle autobotti per gravità, con sistemi a circuito chiuso e collegamento a mezzo di manichetta flessibile”.
L’evento ha avuto origine all’interno del capannone A (Prodotti infiammabili e/o tossici, tossici per l’ambiente, es. Acetato di butile, Toluene, Acetone, Alcool etilico, Alcool metilico, Cicloesano ecc.), in cemento armato e dell’estensione di circa 600 m2, ove avviene l’infustamento dei prodotti infiammabili acetati (tra cui l’acetato di butile coinvolto nell’evento)”. Il capannone è protetto da un impianto di spegnimento manuale a pioggia. Il capannone è classificato area con possibile presenza di atmosfere esplosive (zona 2) ai sensi della Direttiva ATEX. All’interno del capannone i fusti sono stoccati su rulliere, dove permangono in attesa di essere caricati su automezzi tramite carrello elevatore, per il successivo conferimento al cliente”. Vi sono inoltre “due postazioni di carico esattamente simmetriche, denominate D1 e D2, ognuna alimentata da 2 linee di trasferimento prodotti e dotata di 2 pistole di carico, bilancia, pinza di messa a terra, aspiratore ad azionamento manuale”.
Verso le ore 11.30, mentre un operatore autista (dipendente di ditta terza) “stava svolgendo l’attività di infustamento di acetato di butile, o più probabilmente durante lo scolo della linea d’infustamento, si è verificato l’innesco dei vapori all’interno del fusto in lavorazione, che ne ha provocato l’esplosione. Il fondo del fusto si è staccato, per effetto della pressione sviluppata dalla deflagrazione al suo interno, riversando con violenza il liquido contenuto, ormai in fiamme, in parte a terra ed in parte addosso all’operatore che, trasportato in ospedale per ustioni sull’80% del corpo, è deceduto dopo 15 giorni”.
Il conseguente incendio – continua l’intervento – “si è propagato con modesta entità, perché essenzialmente alimentato solo dal liquido sversato. La quantità di liquido coinvolta stimata è dell’ordine del contenuto della linea di travaso, dalla pompa ausiliaria sita in banchina esterna D fino alla pistola di erogazione, quantità corrispondente appunto alla fase finale di infustamento (scolo)”.
L’incendio “è stato domato nell’arco di pochi minuti con l’utilizzo dell’impianto fisso di estinzione, posto nel locale infustamento, e l’utilizzo degli idranti esterni da parte della squadra di emergenza interna. I vigili del fuoco del Comando Provinciale VVF, chiamati in soccorso, sono giunti tempestivamente sul posto quando l’incendio era stato già estinto, ed hanno terminato l’intervento di messa in sicurezza ed emergenza in pochi minuti”.
L’analisi delle cause e delle criticità gestionali all’origine dell’incidente
Riguardo alle cause dell’incidente- come nel precedente articolo, tratto dall’intervento al convegno SAFAP 2018 - riepiloghiamo prima le cause dirette, con riferimento alle ipotesi supportate dall’indagine giudiziaria:
- cause di innesco della miscela infiammabile all’interno del fusto:
- “l’esplosione del fusto è da addebitarsi all’innesco dell’atmosfera infiammabile sviluppatasi al suo interno, che normalmente si forma sopra il pelo libero di un liquido infiammabile, quale è l’Acetato di Normal Butile (punto di infiammabilità + 27C°) in fase di travaso al momento dell’incidente. Infatti i fusti in attesa di riempimento sono pieni d’aria e non appena ha inizio l’introduzione del liquido, questo contestualmente evapora; sia la tensione di vapore dell’Acetato di butile (15 hPa a 20°C) che il rateo di evaporazione (BUAC7=1) sono piuttosto alti, dunque è possibile che quasi immediatamente la concentrazione dei vapori entri nel campo d’infiammabilità, creando di fatto i presupposti per un’esplosione. Detto questo, l’innesco della miscela infiammabile è stato probabilmente dovuto ad una scarica elettrostatica, conseguente ad inefficace contatto della pinza di messa a terra con il fusto. La pinza, infatti, non era dotata di sistema di interblocco, sistema che consente il trasferimento del prodotto nel fusto solo in caso di messa a terra verificata. Inoltre l’attacco della pinza sul bordo verniciato del fusto (unico punto possibile di contatto) riduce ulteriormente l’efficacia della continuità del collegamento equipotenziale, specie se ricostruito più volte a seguito di rigenerazione del fusto stesso. Infine non era presente, nell’area infustamento, alcun sistema di rilevazione di atmosfere potenzialmente pericolose”;
- “l’incidente è avvenuto probabilmente durante lo scolo della linea d’infustamento, con innesco dei vapori all’interno del fusto in lavorazione, che ne ha provocato l’esplosione. Nella fase di scolo dei residui di acetato, infatti, è maggiore il rischio di formazione di atmosfera esplosiva nello spazio interno del fusto sopra al pelo libero della fase liquida, essendo piccola la quantità di liquido infustata. In tali condizioni è più probabile che la miscela infiammabile rientri nel campo di infiammabilità”;
- cause di ‘aggravamento’ danni e mancata mitigazione:
- “importante aspetto emerso a riguardo è legato alla formazione dell’addetto infortunato, il cui mansionario per la qualifica di autista non prevede, come anche dichiarato dal gestore, l’esecuzione di operazioni di infustamento di prodotti”. Era stato assunto con la qualifica di autista di una prima azienda e le condizioni contrattuali “sono state mantenute inalterate” con il passaggio alla seconda azienda. Sotto il profilo formale, “egli non era formato per effettuare operazioni di infustamento di liquidi infiammabili, anche se è possibile che egli fosse a conoscenza delle modalità di esecuzione dell’operazione, almeno per affiancamento con altri operatori”;
- “si osserva inoltre, come ulteriore causa di ‘aggravamento’ che ha portato al decesso dell’operatore, che tale decesso poteva probabilmente essere evitato se lo stesso operatore avesse regolarmente indossato tutti i DPI (tuta, casco …) previsti per l’operazione di infustamento, in particolare la tuta antistatica ignifuga, che avrebbe protetto la parte del corpo seriamente ustionata dalle fiamme. L’operatore deceduto, al momento dell’esplosione, indossava solo scarpe e guanti antistatici, ma era sprovvisto di tuta, casco ed occhiali”.
Veniamo poi alle cause indirette o di radice e alle carenze gestionali SGS connesse.
Infatti “dalle informazioni raccolte e dalla ricostruzione della dinamica dell’evento ipotizzata, è possibile riflettere su possibili cause di radice che sono verosimilmente da ricondursi a carenze gestionali che hanno determinato l’evento”:
- elementi gestionali legati alle cause innesco:
- “necessità di garantire adeguamenti impiantistici e gestionali per la riduzione del rischio per l’attività specifica di infustamento liquidi infiammabili e, in generale, per il trasferimento dei liquidi pericolosi all’interno dello stabilimento. Necessità di adozione delle migliori tecnologie disponibili per i sistemi di sicurezza adottati in tale fase, nonché di misure di sicurezza adeguate in linea anche con le prescrizioni” del CTR (Comitato Tecnico Regionale) “formulate in merito all’incidente:
- prevedere, tra le operazioni preliminari all’infustamento, la verifica dell’effettivo collegamento equipotenziale del contenitore mobile da riempire. Qualora tale operazione avesse esito negativo, deve essere precluso l’avvio delle pompe utilizzate per l’infustamento;
- prevedere l’interdizione dell’operazione di infustamento anche per le seguenti condizioni:
- “necessità di garantire adeguamenti impiantistici e gestionali per la riduzione del rischio per l’attività specifica di infustamento liquidi infiammabili e, in generale, per il trasferimento dei liquidi pericolosi all’interno dello stabilimento. Necessità di adozione delle migliori tecnologie disponibili per i sistemi di sicurezza adottati in tale fase, nonché di misure di sicurezza adeguate in linea anche con le prescrizioni” del CTR (Comitato Tecnico Regionale) “formulate in merito all’incidente:
- malfunzionamento o mancata attivazione dell’impianto di aspirazione a servizio dell’area di infustamento;
- rilevazione di atmosfere infiammabili nella suddetta area mediante installazione di un sistema di rilevazione di vapori infiammabili;
- raggiungimento del massimo grado di riempimento nel contenitore mobile in funzione della sostanza da infustare”.
- “necessità di revisione dell’analisi di sicurezza eseguita dall’azienda, con considerazione di tutte le ipotesi incidentali in area infustamento, inclusa la fase finale di scolo; una corretta e completa analisi avrebbe portato alla individuazione di misure di sicurezza più adeguate a prevenire e/o mitigare l’evento occorso.
- necessità di aggiornare il documento di valutazione del rischio esplosione garantendo l’adeguatezza, rispetto alla classificazione delle aree con pericolo di esplosione, di tutte le attrezzature in esse installate”.
- elementi gestionali legati alle cause di ‘aggravamento’ danni e mancata mitigazione dell’evento:
- “necessità di garantire una corretta definizione di ruoli e mansioni sia del personale operativo (coordinamento ed esecuzione lavori) che del personale dirigente (supervisione dei lavori);
- necessità di rivedere piano e attività di formazione ed addestramento del personale interno ed esterno, anche ai fini di migliorare l’interfaccia operatore-impianto, in relazione ai ruoli e mansioni ridefiniti secondo il punto precedente”.
Si sottolinea poi che un’adeguata implementazione di SGS “prevede, in termini di formazione dei lavoratori interni ed esterni, che il personale di azienda sia stato formato sulle attività di analisi delle situazioni incidentali, per l'individuazione delle cause di tipo tecnico, organizzativo e gestionale, che a seguito delle attività di formazione ed addestramento siano verificati l’efficacia dell’addestramento ed il grado di consapevolezza raggiunto, e che anche le ditte terze che lavorano in stabilimento abbiano opportunamente svolto l'attività di formazione per i propri addetti e ne venga verificata l’efficacia”.
E in termini di fattore umano ed interfaccia operatore-impianto, l’SGS “prevede l’esistenza e l’attuazione di programmi di addestramento ed esercitazioni per migliorare il comportamento dell’operatore; che l’organizzazione dei turni di lavoro e delle mansioni siano tali da considerare i rischi dovuti a stress lavoro-correlato a cui sono sottoposti i lavoratori; e che siano posti in atto meccanismi di verifica del mantenimento delle idonee condizioni psicofisiche”.
In definitiva questo caso e quello raccontato in un precedente articolo sottolineano come il rischio di sovrapressione all’interno di apparecchiature che lavorano con sostanze pericolose, “indipendentemente dalle normali condizioni operative e dai parametri operativi di esercizio”, vada comunque “considerato nell’analisi di rischio effettuata dal gestore, ed analizzato come anomalia di processo e di gestione, al fine consentire la formulazione tutte le necessarie misure tecniche e gestionali preventive per il verificarsi di esplosioni, conseguenti al suddetto rischio”.
Rimandiamo, in conclusione, alla lettura integrale dell’intervento non solo per la presenza di ulteriori dettagli e immagini, ma anche perché all’intervento è allegata una tabella sulle criticità gestionali ed elementi comuni emersi dal raffronto dei due casi incidentali.
Tiziano Menduto
Scarica il documento da cui è tratto l'articolo:
Inail, Dipartimento innovazioni tecnologiche e sicurezza degli impianti, prodotti e insediamenti antropici, “ SAFAP 2018 - Sicurezza e affidabilità delle attrezzature a pressione. La gestione del rischio dalla costruzione all’esercizio a 130 anni dal primo decreto sulla sicurezza delle caldaie a vapore”, atti del convegno SAFAP 2018 a cura di Francesca Ceruti e Daniela Gaetana Cogliani, edizione 2018 (formato PDF, 29.42 MB).
Vai all’area riservata agli abbonati dedicata a “ La sicurezza e l’affidabilità delle attrezzature a pressione”.

I contenuti presenti sul sito PuntoSicuro non possono essere utilizzati al fine di addestrare sistemi di intelligenza artificiale.
Per visualizzare questo banner informativo è necessario accettare i cookie della categoria 'Marketing'