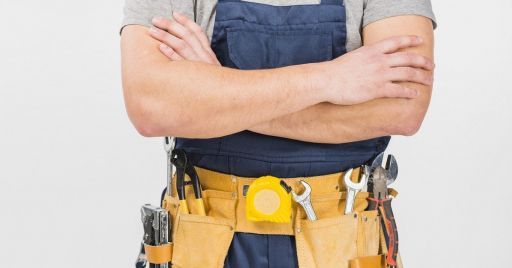
Per utilizzare questa funzionalità di condivisione sui social network è necessario accettare i cookie della categoria 'Marketing'.
Imparare dagli errori: ancora sulle cattive prassi nella manutenzione
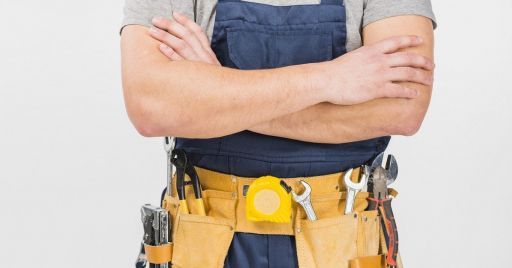
Brescia, 14 Mar – Nell’articolo “ Imparare dagli errori: la manutenzione in mancanza di idonee procedure”, una puntata della nostra rubrica dedicata al racconto degli infortuni professionali, abbiamo sottolineato come una delle cause dei tanti infortuni nelle attività di manutenzione sia l’assenza, in molti casi, di idonee procedure e prassi.
Nelle attività di manutenzione è, infatti, importante – come ricordato nel “ Factsheet n. 88: Manutenzione sicura — Lavoratori sicuri” - “seguire le prassi di lavoro sicuro sviluppate in fase di pianificazione”.
È necessario pianificare le attività di manutenzione e il piano di lavoro “deve essere seguito anche quando il tempo è scarso: le procedure abbreviate possono essere molto costose e possono produrre incidenti, infortuni o danni ai beni”. Ed è importante “avvisare i supervisori e/o consultare altri esperti nel caso in cui si verificasse qualche evento imprevisto”. Infatti “oltrepassare l’ambito delle proprie abilità e competenze potrebbe causare un incidente molto grave”.
Torniamo, dunque, a parlare anche oggi di manutenzione, con particolare riferimento alla mancanza di idonee prassi, presentando un caso di infortunio presente nell’archivio di INFOR.MO., strumento per l'analisi qualitativa dei casi di infortunio collegato al sistema di sorveglianza degli infortuni mortali e gravi.
Questi gli argomenti trattati nell’articolo:
- Un esempio di infortunio nelle attività di manutenzione
- La manutenzione, il processo di progettazione e i rischi specifici
Un esempio di infortunio nelle attività di manutenzione
Il caso che presentiamo oggi si sofferma su un lavoratore, responsabile della manutenzione delle macchine e delle attrezzature dell'impresa, che viene chiamato da un collega che segnala il mancato funzionamento di un carroponte da 8 tonnellate in un reparto.
Il lavoratore, responsabile della manutenzione, interviene affiancato da un collega.
Dopo essersi portato alla quota utile per la riparazione con l'ausilio di un ponte mobile, azionato dal collega di supporto, si posiziona sotto il carroponte per poter eseguire le attività di manutenzione.
Un terzo lavoratore a terra, che tiene la pulsantiera mobile del carroponte, ha ordine di verificare che i comandi dell'accensione siano disattivati, prima dell'inizio della manutenzione.
Dopo aver riparato il guasto il manutentore presente sulla piattaforma aerea si accovaccia al di sotto del livello del parapetto della struttura metallica, ovvero al di sotto dello spazio di manovra del carroponte, chiedendo al collega a terra di azionare la pulsantiera per verificarne il funzionamento.
L'operazione va a buon fine ed il carroponte viene nuovamente arrestato dal lavoratore a terra, consentendo al manutentore di rialzarsi per radunare gli attrezzi all'interno della struttura metallica, al fine di poter tornare a terra.
Improvvisamente il carroponte riprende il movimento, investendo il manutentore che viene preso parzialmente a contrasto tra il carroponte e una mensola.
Attirato dalle urla, il manovratore del carroponte a terra inverte immediatamente il senso di marcia della macchina, mentre il lavoratore che conduce il ponte mobile lo abbassa, consentendo all'infortunato di arrivare a terra per il soccorso.
Le indagini successive hanno rilevato che l'infortunato, pur “esperto di manutenzione e con esperienza consolidata negli anni”, “non ha rispettato le procedure di sicurezza, ed in particolare l'obbligo di interrompere l'alimentazione elettrica degli impianti prevedendo la messa in sicurezza mediante chiusura con lucchetto, nonché portare con sé la pulsantiera per azionarne direttamente i comandi, come previsto dalle buone prassi”.
L'infortunato, “sebbene a conoscenza delle procedure di sicurezza poiché qualificato come manutentore esperto, non ha rispettato la sequenza delle fasi di effettuazione dell'intervento di manutenzione, ovvero per fare più in fretta non ha tolto l'alimentazione elettrica, e comunque non è sceso a terra per effettuare le prove di funzionamento, bensì le ha effettuate nei pressi dell'area di manovra del carroponte”.
Inoltre era necessario “avere il comando diretto del carroponte, portando con sé la pulsantiera”.
Questi, dunque, i fattori causali individuati, già esplicitati sopra:
- “il carroponte ha ripreso improvvisamente il moto investendo l'infortunato”;
- “l'infortunato, sebbene a conoscenza delle procedure di sicurezza poiché qualificato come manutentore esperto, non ha rispettato la sequenza delle fasi di effettuazione dell'intervento di manutenzione, ovvero per fare più in fretta non ha tolto l'alimentazione elettrica, e comunque non è sceso a terra per effettuare le prove di funzionamento, bensì le ha effettuate nei pressi dell'area di manovra del carroponte. era inoltre necessario avere il comando diretto del carroponte, portando con sé la pulsantiera”.
La manutenzione, il processo di progettazione e i rischi specifici
Per avere qualche spunto per il miglioramento della prevenzione degli infortuni nelle attività manutentive possiamo fare riferimento al contenuto del documento Inail “ La manutenzione per la sicurezza sul lavoro e la sicurezza nella manutenzione”.
Nel documento si segnala, ad esempio, che una buona pratica riguarda l’eliminazione dei rischi in fase di progettazione.
Infatti, “uno dei modi migliori per prevenire e controllare i rischi (anche quelli legati alla manutenzione) è affrontarli all’inizio del processo di progettazione di ambienti di lavoro, attrezzature e impianti”.
In particolare considerare la manutenzione durante la fase di progettazione “consente di eliminare i pericoli ad essa associati o di minimizzare il potenziale di lesioni durante la manutenzione o la riparazione di un elemento, ad esempio:
- nel caso di un’attrezzatura, è possibile adottare sistemi automatici di rilevamento di taluni pericoli, o interruttori interbloccati al fine di prevenire qualsiasi avviamento imprevisto durante i lavori di manutenzione; ad esempio la procedura LOTO (lockout-tagout) garantisce che macchine ed impianti siano de-energizzati in maniera appropriata e non possano essere rimessi in funzione se non in condizioni sicure dal lavoratore o dai lavoratori che ne hanno operato lo spegnimento;
- nel caso di luoghi di lavoro, è possibile coinvolgere i lavoratori che dovranno svolgere i lavori di manutenzione nella loro progettazione, in modo da garantire un miglioramento della salute e della sicurezza delle operazioni di manutenzione e il loro regolare svolgimento (ad esempio: è possibile utilizzare un modello virtuale per consentire ai lavoratori di esaminare, spostarsi e valutare la propria area di lavoro futura prima che sia costruita, eliminando alcuni dei fattori di rischio ergonomici, liberando spazio per compiti specifici, garantendo un accesso sicuro alle aree di lavoro, adottando isolamenti acustici per le zone dove si svolgono procedure particolarmente rumorose in modo da limitare l’esposizione al rumore dei lavoratori e così via)”.
Il documento ricorda anche che la valutazione del rischio durante le operazioni di manutenzione può essere un compito particolarmente difficile e che “può richiedere inventiva”, a causa delle incertezze del lavoro manutentivo: può capitare, infatti, di “iniziare un certo intervento di manutenzione correttiva e scoprire che ulteriori interventi non previsti sono necessari”.
Il documento presenta poi vari pericoli (fisici, ergonomici, chimici, biologici, …) per il manutentore, ma affronta anche alcuni rischi specifici delle attività di manutenzione:
- “Ad esempio, quando si effettua manutenzione su di un macchinario che fa parte di una catena di produzione, può capitare, mentre è in corso l’esecuzione di un processo, di dover operare in stretto contatto con organi in movimento o parti sotto tensione. Durante il normale funzionamento dei macchinari sono il sistema automatico di sicurezza e le misure di protezione che riducono solitamente la probabilità di un errore umano che possa portare a incidenti. Tuttavia, nelle condizioni in cui si trovano ad operare i lavoratori che eseguono la manutenzione, la probabilità che possa aversi un contatto diretto tra il lavoratore e gli organi in movimento o le parti sotto tensione non può essere ridotta più di tanto.
- La manutenzione spesso comporta un lavoro insolito o attività non di routine e viene spesso eseguita in condizioni eccezionali, ad esempio lavorando in spazi ristretti.
- Le operazioni di manutenzione potrebbero riguardare lo smontaggio e il rimontaggio, di attrezzature complesse: in situazioni simili il rischio di errore umano cresce e aumenta il pericolo di incidenti.
- In caso di appalti per l’esecuzione di lavori di manutenzione, i lavoratori inviati ad eseguire interventi presso le società appaltanti si trovano spesso a dover cambiare attività lavorativa e ambiente di lavoro, e ciò ha come risultato un incremento del rischio di commettere errori che possano dar luogo ad incidenti. Inoltre, gli appalti multipli e i subappalti sono fattori aggravanti in termini di sicurezza e salute, infatti numerosi incidenti riguardano attività di manutenzione in appalto multiplo o subappalto.
- In alcune realtà produttive i tempi per l’esecuzione della manutenzione devono essere necessariamente ridotti, in particolare quando sono coinvolti rallentamenti o arresti della produzione: in casi simili, le riparazioni ed il ripristino della produzione divengono attività ad alta priorità, ed i lavoratori si trovano a dover operare sotto la pressione del tempo”.
Rimandiamo alla lettura integrale del documento Inail che, riguardo alle attività di manutenzione, si sofferma anche sulla valutazione del rischio e sull’utilità dei sistemi di gestione della salute e sicurezza sul lavoro.
Sito web di INFOR.MO.: nell’articolo abbiamo presentato la schede di Infor.mo. 17022 (archivio incidenti 2002/2021).
Tiziano Menduto
Scarica le schede da cui è tratto l'articolo:

I contenuti presenti sul sito PuntoSicuro non possono essere utilizzati al fine di addestrare sistemi di intelligenza artificiale.
Per visualizzare questo banner informativo è necessario accettare i cookie della categoria 'Marketing'