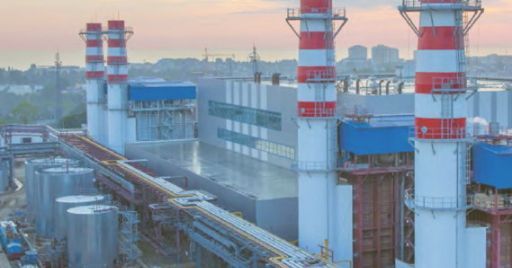
Per utilizzare questa funzionalità di condivisione sui social network è necessario accettare i cookie della categoria 'Marketing'.
SAFAP 2023: la gestione dell'invecchiamento delle apparecchiature critiche
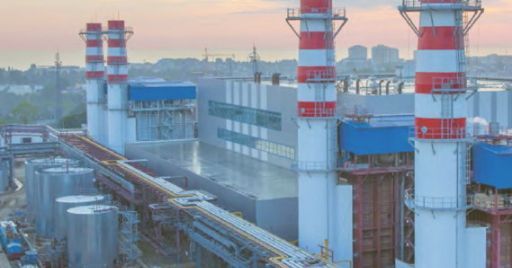
Brescia, 28 Nov – Come abbiamo ricordato in molti articoli sui rischi delle attrezzature a pressione, i convegni SAFAP (Sicurezza ed affidabilità delle attrezzature a pressione) sono un importante appuntamento annuale di confronto tecnico-scientifico rivolto a tutti coloro (ricercatori, progettisti, fabbricanti, impiantisti, esercenti, esperti della sicurezza, addetti alle verifiche, ispettori, …) che operano nel settore delle attrezzature a pressione, degli impianti di processo, dei generatori di vapore e degli impianti a rischio d’incidente rilevante.
Dal 22 al 24 novembre 2023 si è tenuta la decima edizione del convegno SAFAP “Sicurezza e affidabilità delle attrezzature a pressione e degli impianti di processo” che ha previsto una sessione plenaria, due workshop e varie sessioni tematiche dedicate ai vari aspetti della vita delle attrezzature a pressione (dalla progettazione alla fabbricazione, dall’ispezione alla manutenzione) e della sicurezza degli impianti di processo con un focus al controllo del pericolo di incidenti rilevanti (PIR).
Per far conoscere i risultati di questa decima edizione, e migliorare la sicurezza delle attrezzature, il Dipartimento innovazioni tecnologiche e sicurezza degli impianti, prodotti e insediamenti antropici (DIT) dell’Inail ha raccolto, come ogni anno, in un unico volume – dal titolo “SAFAP 2023 - Sicurezza e affidabilità delle attrezzature a pressione e degli impianti di processo” – tutte le relazioni presentate durante i tre giorni di convegno.
Ci soffermiamo oggi, in particolare, su una relazione che fa riferimento all’utilizzo di nuove tecnologie per migliorare la sicurezza.
Infatti – si legge nell’abstract della relazione – nell'industria di processo (le attività in cui attraverso processi chimico-fisici vengono modificate le caratteristiche delle sostanze in ingresso, trasformandole in toto o in parte) “tutti i sistemi di contenimento primari sono soggetti a forme di deterioramento”. E per gestire il rischio di incidenti rilevanti dovuti a tale fenomeno, “la normativa vigente prevede controlli periodici per verificare le condizioni di salute (invecchiamento dell’apparecchiatura)”.
Per supportare l'ispezione nell'affrontare questo compito, la relazione racconta che “è stato progettato e sviluppato un Sensore Virtuale. Si tratta di un sistema, composto da hardware e software, che utilizza modelli matematici e la Realtà Aumentata per assistere le ispezioni in campo per il monitoraggio e la previsione dell’invecchiamento delle apparecchiature”.
L’articolo si sofferma sui seguenti argomenti:
- Le nuove tecnologie e il controllo del rischio di incidenti rilevanti
- I sensori virtuali e il deterioramento dell'attrezzatura critica
- La realtà aumentata, l’interfaccia user-friendly e le ispezioni
Le nuove tecnologie e il controllo del rischio di incidenti rilevanti
Nell’intervento “L'utilizzo della Realtà Aumentata per la gestione dell'invecchiamento delle apparecchiature critiche attraverso un Sensore Virtuale” – a cura di G. Ancione e R. Saitta (Università di Messina, Dipartimento di Ingegneria), P. Bragatto (Università Campus Bio-Medico di Roma, Dipartimento di Ingegneria) e G. Fiumara (Università di Messina, Dipartimento di Scienze Matematiche e Informatiche, Scienze Fisiche e Scienze della Terra) – si ricorda che le tecnologie innovative come l'Internet of Things (IoT), l' intelligenza artificiale, big data, il cloud computing, i sistemi cyber-fisici, l'interconnettività, la realtà aumentata, ecc. “hanno caratterizzato lo sviluppo dell'Industria 4.0 attraverso l'integrazione di sistemi fisici e digitali”. E un aspetto importante da menzionare è il “potenziale supporto per il miglioramento della gestione della sicurezza, anche se attualmente ci sono solo pochi studi che analizzano l'integrazione tra la gestione della sicurezza e l' Industria 4.0”.
Tuttavia se le interazioni tra macchine e macchine e tra esseri umani e macchine rappresentano aspetti fondamentali di questo processo di digitalizzazione connesso all’evoluzione dell’Industria 4.0, queste interazioni “non sono prive di svantaggi”.
Si segnala che le tecnologie emergenti e sperimentali “causano un profondo cambiamento nella società, che ha bisogno di tempo per adattarsi e normalizzarsi attraverso nuovi paradigmi, nuove procedure, nuove leggi sul lavoro. Questo richiede alle aziende di aggiornarsi continuamente, ma spesso diventa insostenibile per la maggior parte di loro, soprattutto per le aziende medio-piccole”.
Inoltre questi sistemi “creano una dipendenza assoluta dalla tecnologia poiché all'interno di queste interazioni, le macchine non rappresentano più solo il braccio che svolge il lavoro pesante, ripetitivo e/o pericoloso, ma giocano sempre più un ruolo decisionale”.
Particolare attenzione deve essere poi data agli stabilimenti disciplinati dalla direttiva Seveso, “nei quali la fuoriuscita di sostanze pericolose potrebbe causare gravi incidenti, i cosiddetti incidenti rilevanti (cioè, incendi, esplosioni e dispersioni tossiche) che incidono sulle persone e sull'ambiente”.
I relatori, che riportano varie soluzioni innovative per migliorare il controllo del rischio di incidenti rilevanti, indicano che nell'ambito di un recente progetto di ricerca è stato sviluppato un “sensore virtuale per elaborare e visualizzare informazioni relative al deterioramento di apparecchiature critiche; inoltre, esso produce stime prognostiche del tasso di corrosione, della probabilità del pit critico, l'evoluzione della corrosione del materiale e la vita utile residua (RUL) dell'attrezzature”. E’ stata poi condotta un'indagine “sull'interazione uomo-macchina nell'uso di questo dispositivo; questo lavoro ha portato a un'interfaccia user-friendly, che ha migliorato l'utilizzabilità del software rendendolo accessibile anche al personale non esperto in tecnologie avanzate”. E lo scopo di questa relazione è proprio quello di “presentare l'implementazione del sensore virtuale minimizzando gli errori associati all'interazione uomo-macchina”.
I sensori virtuali e il deterioramento dell'attrezzatura critica
Gli autori indicano che un sensore virtuale per la gestione dell'invecchiamento “è uno strumento che supporta gli ispettori nelle strutture a rischio di incidente rilevante. Gli ispettori hanno bisogno di comprendere il livello effettivo di deterioramento dell'attrezzatura critica, acquisire informazioni che non possono essere trovate con una sola ispezione visiva e infine elaborare le metriche legate allo stato di invecchiamento e all'adeguatezza della gestione dell'invecchiamento”.
E il sistema presentato “è stato progettato per raccogliere varie informazioni, elaborare i dati acquisiti, produrre stime prognostiche su: velocità di corrosione, probabilità di pit critico, evoluzione della superficie di corrosione, tempo di vita residuo (RUL) dell'attrezzatura e infine, permette la visualizzazione dei risultati utilizzando la realtà aumentata”.
Si segnala poi che per testare il sensore virtuale “è stato utilizzato un serbatoio di stoccaggio di idrocarburi a tetto fisso all’interno di un impianto Seveso”, un serbatoio realizzato in acciaio al carbonio che immagazzina diesel.
La realtà aumentata, l’interfaccia user-friendly e le ispezioni
Veniamo direttamente alle conclusioni degli autori.
Come già detto in apertura il sensore virtuale è uno strumento “utile per l'ispettore per accedere alle informazioni necessarie su campo durante le ispezioni”. In particolare, la realtà aumentata (AR) fornisce “informazioni sullo stato di integrità delle parti dell'attrezzatura che non possono essere osservate direttamente durante un'ispezione visiva. Inoltre, permette la produzione di metriche prognostiche correlate all'invecchiamento oltre al loro aggiornamento e archiviazione”.
Questo sistema è stato dotato di “una interfaccia user-friendly grazie allo studio dell'interazione uomo-macchina (HMI) che ha supportato il processo di implementazione e ha permesso di migliorare l'usabilità del software rendendolo accessibile anche a personale non esperte di tecnologie avanzate”.
Si indica poi che, attualmente, il sensore virtuale è “progettato per ispezionare serbatoi di stoccaggio molto grandi per la gestione dell'integrità di alcune parti di questo tipo di attrezzatura”.
A questo proposito si segnala che il fondo del serbatoio “non è facile da monitorare, poiché la sua ispezione richiede che il serbatoio venga svuotato e poi pulito per effettuare le misurazioni dello spessore”. Inoltre “queste attività vengono eseguite a intervalli di tempo lunghi per evitare prolungate interruzioni e ripetute esposizione dell'ispettore ad ambienti insalubri”.
Il sensore virtuale risulta “particolarmente significativo nei casi in cui sia difficile interrompere il funzionamento del sistema per monitorare una parte di esso (come nel caso del fondo dei serbatoi)”.
Si segnala tuttavia che l'attuale sperimentazione è stata condotta in laboratorio e “in uno stabilimento reale, l’orografia del terreno e le condizioni meteorologiche potrebbero influenzare l'accuratezza ed efficacia dell'uso della tecnologia”. E si rende necessario un test in un vero stabilimento.
In ogni caso si sottolinea che “la visualizzazione della mappa di corrosione, combinata con la stima della RUL” (vita utile residua) “e gli altri parametri legati all'invecchiamento, consente all'ispettore di concentrare l'attenzione sui punti critici quando si trova in campo”. Il sistema (sensore virtuale) permette poi di “combinare deduzioni visive con previsioni ottenute dai modelli al fine di comprendere l’evoluzione prevista del fenomeno, anche in base a come questo fenomeno viene realmente gestito”.
Concludiamo rimandando alla lettura integrale dell’intervento che riporta molte altre indicazioni sulla ricerca e sulle soluzioni sperimentate, ad esempio con riferimento all’architettura del sistema, alle interazioni uomo-macchina, all’interfaccia grafica del sensore virtuale e all’utilizzo della realtà aumentata.
Tiziano Menduto
Scarica il documento da cui è tratto l'articolo:
Inail, Dipartimento innovazioni tecnologiche e sicurezza degli impianti, prodotti e insediamenti antropici, “ SAFAP 2023 - Sicurezza e affidabilità delle attrezzature a pressione e degli impianti di processo”, atti del convegno SAFAP 2023, editing di Francesca Ceruti e Daniela Gaetana Cogliani, edizione 2023 (formato PDF, 32.18 MB).
Vai all’area riservata agli abbonati dedicata a “ 2023: le novità sulla sicurezza e affidabilità di attrezzature a pressione e impianti di processo”.

I contenuti presenti sul sito PuntoSicuro non possono essere utilizzati al fine di addestrare sistemi di intelligenza artificiale.
Per visualizzare questo banner informativo è necessario accettare i cookie della categoria 'Marketing'