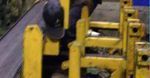
Per utilizzare questa funzionalità di condivisione sui social network è necessario accettare i cookie della categoria 'Marketing'
Per visualizzare questo banner informativo è necessario accettare i cookie della categoria 'Marketing'
Storie di infortunio: bastava uno sguardo
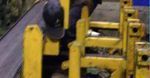
Grugliasco (TO), 1 Lug – Il Centro regionale di Documentazione per la Promozione della Salute della Regione Piemonte ( Dors) raccoglie storie d'infortunio rielaborate dagli operatori dei Servizi PreSAL delle ASL piemontesi a partire dalle inchieste di infortunio, con la convinzione che conoscere come e perché è accaduto sia una condizione indispensabile per proporre soluzioni efficaci per la prevenzione. In questa storia, dal titolo “Bastava uno sguardo” (a cura di Luisa Barbieri, Silvia Nobile, Servizio Pre.S.A.L. della Asl VCO) viene presentato un incidente all’interno di un impianto per l’impaccatura e il confezionamento di laminati in ferro.
Questo articolo è pubblicato sotto una Licenza Creative Commons.
Che cosa
Un operaio rimane schiacciato all’interno di un impianto per l’impaccatura e il confezionamento di laminati in ferro, riportando un trauma da schiacciamento con amputazione sub totale della gamba destra e del piede destro e l’ustione dell’addome e del braccio destro, rischiando di perdere la vita.
Chi
Francesco, un operaio italiano di 35 anni, era assunto a tempo indeterminato da circa 4 anni come addetto alla laminazione del ferro e alla manutenzione di un piccolo impianto di laminazione di profili metallici.
Dove e quando
L’evento si è verificato nel 2006, in un pomeriggio di Novembre, in provincia del Verbano Cusio Ossola, nella zona industriale di un comune di circa 3.500 abitanti situato nella Valle dell’Ossola, all’interno di un’azienda che produce laminati in acciaio di piccole dimensioni.
In particolare, l’infortunio è avvenuto alla fine del ciclo produttivo nel reparto di impaccatura e confezionamento dei laminati. Dopo essere stato lavorato a caldo, il materiale viene trasportato tramite alcuni trasferitori a catena in “sacche fisse di raccolta”.
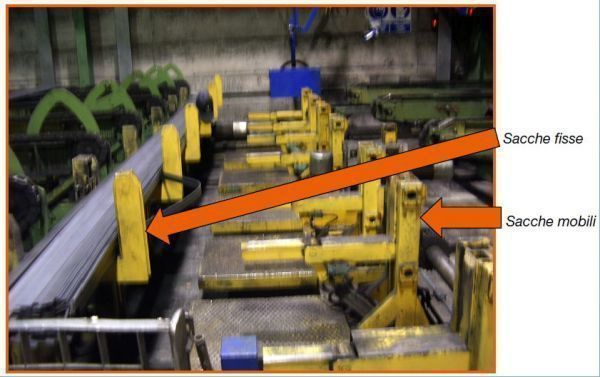
Le sacche fisse di raccolta sono strutture metalliche all’interno delle quali vengono posizionati i prodotti laminati. A queste seguono le cosiddette “sacche mobili” che, sostanzialmente identiche alle fisse, hanno il compito di prelevare il materiale lavorato e trasferirlo nella zona di pesatura in modo che sia legato tramite una macchina reggiatrice e trasferito al magazzino.
Come
Alle ore 18.30, una barra metallica fuoriusciva dalla culla della sacca fissa e costituiva un potenziale incaglio che avrebbe potuto bloccare l’intero ciclo produttivo.
Angelo, assunto da soli cinque giorni con contratto di lavoro interinale, ha subito chiamato Francesco per effettuare insieme le operazioni necessarie al riposizionamento corretto della barra. Per riposizionarla Francesco e Angelo, si sono recati presso l’ultima sacca fissa di raccolta, distante sette metri dal quadro comandi.
I due lavoratori hanno attraversato un passaggio pedonale largo circa tre metri e delimitato alle due estremità da barriere immateriali (fotocellule). Passando tra le due fotocellule, il macchinario è andato in blocco (emergenza).
Dopo aver brevemente conversato con Francesco, Angelo è ritornato al quadro comandi dell’impaccatrice posto nelle immediate vicinanze delle sacche, su un pulpito sopraelevato di 40 centimetri. Dal pulpito non erano presenti ostacoli che limitassero la visibilità dell’operatore addetto alle manovre.
Angelo ha premuto il pulsante giallo di “ripristino barriera” che lampeggiava e, sollevando il pulsante rosso di emergenza, ha disattivato il blocco; premendo poi il pulsante “start ciclo”, ha messo in moto le sacche mobili.
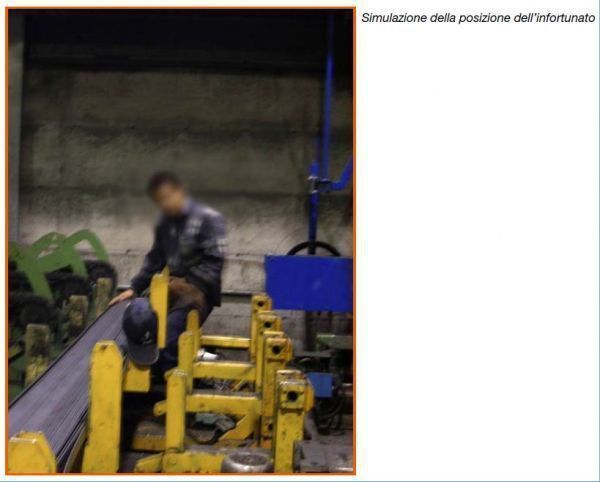
Le sacche mobili si sono spostate in direzione di Francesco che si trovava ancora nell’ultima sacca fissa di raccolta, intento a martellare la barra mal posizionata. Francesco non si è accorto del movimento delle sacche, anche perché indossava gli otoprotettori.
“Inesperto e concentrato sul lavoro che dovevo fare, sono intervenuto sui comandi con lo sguardo rivolto su di essi, non mi sono più curato di accertarmi della sua presenza. Penso che Francesco fosse non in una posizione completamente eretta, tra i macchinari che lo nascondevano parzialmente. Mi sono accorto di Francesco quando lui ha gridato e quindi la macchina lo stava già schiacciando.”
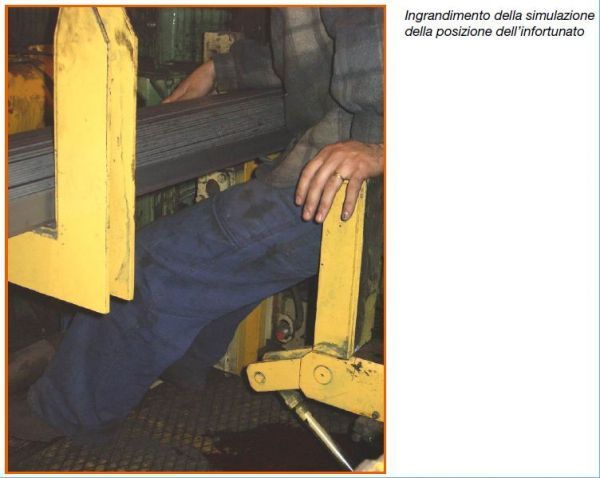
Quando Angelo ha sentito le urla del collega, le sacche mobili stavano già schiacciando Francesco contro quelle fisse.
“Mentre venivo schiacciato ho urlato ad Angelo di fare qualcosa, di premere qualche pulsante ma lui mi guardava, non faceva nulla e gridava “No, no” come preso dal panico.”
Perché
Angelo ha riavviato l’impianto senza guardare nella direzione delle sacche, poiché era intento sulla sequenza di pulsanti da premere e ha dato per scontato che Francesco avesse già terminato l’operazione che doveva svolgere.
Cosa si è appreso dall’inchiesta
Da un esame successivo dell’impaccatrice, si è rilevato che il quadro comandi, deputato alla messa in moto della sacca mobile, era privo di un dispositivo di arresto di emergenza dotato di selettore a chiave rimovibile che serve a far sì che, chi entra nella zona pericolosa (in questo caso Francesco), possa svolgere l’ attività manutentiva evitando l’azionamento improprio di un altro lavoratore (in questo caso Angelo).
Tenendo conto della sequenza di azioni necessarie per avviare il macchinario, si deduce che non poteva essere riattivato da Angelo per errore.
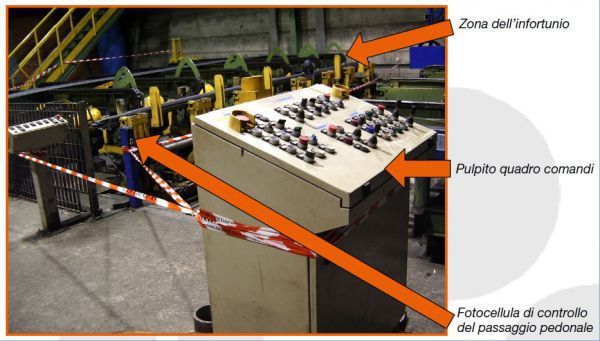
Indicazioni per la prevenzione
Considerata l’entità del danno che il macchinario può causare, il quadro comandi per la messa in moto della sacca mobile avrebbe dovuto prevedere un dispositivo facilmente accessibile dal personale addetto alla manutenzione che assicurasse la posizione di arresto della macchina e dei suoi organi. Un dispositivo di questo tipo potrebbe essere un fungo di arresto di emergenza dotato di chiave rimovibile esclusivamente dal personale autorizzato.
L’azienda avrebbe dovuto, inoltre, stilare delle procedure di sicurezza dove il personale addetto alla manutenzione, prima di accedere alla zona pericolosa, debba bloccare la macchina ed estrarre la chiave dal selettore, custodendola fino alla conclusione dell’intervento. Ciò avrebbe impedito il verificarsi dell’infortunio nonostante una possibile azione “impropria” da parte di altri lavoratori.
Sebbene il compito da svolgere (premere tre pulsanti in sequenza) fosse semplice, Angelo, lavoratore interinale in azienda da soli cinque giorni, non era in grado di far fronte a una situazione lavorativa che altri lavoratori più esperti potevano considerare consueta. Questo evento ribadisce l’importanza per i lavoratori neo-assunti di essere affiancati e addestrati nel corso delle diverse fasi lavorative, evitando lo svolgimento in autonomia di attività che possano comportare rischi elevati.
Luisa Barbieri, Silvia Nobile
SPreSAL della ASL VCO
Fonte: Dors.
