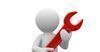
Per utilizzare questa funzionalità di condivisione sui social network è necessario accettare i cookie della categoria 'Marketing'
Questo articolo è pubblicato sotto una Licenza Creative Commons.
Per visualizzare questo banner informativo è necessario accettare i cookie della categoria 'Marketing'
Buone prassi per pianificare la manutenzione in azienda
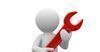
Roma, 23 Apr – La definizione di un piano di manutenzione preventiva, l’implementazione di un software dedicato e la formazione e sensibilizzazione del personale incaricato possono essere soluzioni idonee alla prevenzione delle conseguenze correlate alla mancata manutenzione e l’errata manutenzione di macchinari, attrezzature, impianti e strumenti. Conseguenze che possono determinare incidenti o “ near-misses” con la conseguenza di infortuni ai lavoratori e danni alla produzione.
Questo è quanto suggerisce una buona prassi, dal titolo “Pianificazione della Manutenzione, Utilizzo di Software dedicato e Formazione per Addetti Manutenzione”, validata dalla Commissione Consultiva Permanente per la salute e sicurezza sul lavoro il 30 maggio 2012.
Nei documenti allegati alla scheda della buona prassi, applicata all’interno dell’azienda Iscar Italia s.r.l., si segnala che “la gestione degli impianti, dei mezzi, dei macchinari e delle attrezzature è affidata al Rappresentante della Direzione e ai Responsabili delle attività di manutenzione interessati per le rispettive competenze, con il supporto del Direttore Amministrativo per gli assetti amministrativo-contabili, che provvedono alla loro costante idoneità all'uso per cui sono previsti. Allo scopo, il Rappresentante della Direzione e i Responsabili delle attività di manutenzione interessati organizzano tutto quanto è necessario per assicurare la massima efficienza, idoneità e sicurezza degli impianti, dei mezzi, dei macchinari e delle attrezzature utilizzati dall'Azienda”.
La gestione di impianti, mezzi e macchinari in sicurezza si sostanzia nelle “seguenti attività:
- individuare, con il supporto delle Funzioni specialistiche, quegli impianti, quei mezzi, quei macchinari e quelle attrezzature, che inficiando il regolare svolgimento delle attività influenti le prestazioni qualitative, ambientali e di salute e sicurezza aziendali, sono da sottoporre ad interventi di manutenzione preventiva;
- predisporre opportune schede, associate agli impianti, ai mezzi, ai macchinari e alle attrezzature di cui al punto precedente, con le quali programmare gli interventi di manutenzione da effettuare e registrare quelli effettuati;
- predisporre, con il supporto delle Funzioni Specialistiche, opportune indicazioni scritte qualora la loro mancanza possa inficiare negativamente gli aspetti relativi alla gestione operativa della manutenzione e alle modalità di conduzione finalizzate ad un uso corretto ed in sicurezza degli impianti, dei mezzi, dei macchinari o delle attrezzature utilizzati;
- individuare specifiche modalità comportamentali per la verifica dell'idoneità all'uso di quelle attrezzature per le quali non sono di utilità interventi di manutenzione preventiva;
- individuare le Organizzazioni Esterne in grado di eseguire attività specialistiche di manutenzione sugli impianti, sui macchinari, sui mezzi, sulle attrezzature e sugli eventuali strumenti di misura presenti sugli stessi”.
Veniamo alle varie fasi attuative della buona prassi.
La prima fase ha previsto il censimento degli impianti, dei mezzi, dei macchinari e delle attrezzature e la gestione di una Scheda di Manutenzione.
Riguardo a questa fase “i Responsabili delle attività di manutenzione gestiscono e tengono aggiornato un apposito Elenco Impianti Mezzi Macchinari ed Attrezzature in dotazione all'Azienda, che sottopongono alla verifica del Rappresentante della Direzione, con indicazione delle informazioni essenziali di carattere anagrafico e tecnico per la loro completa ed univoca identificazione. In particolare, agli impianti, ai mezzi, ai macchinari e alle attrezzature viene assegnato, quando necessario, anche un codice identificativo riportato sull’impianto, sul mezzo, sul macchinario o sull’attrezzatura stessi”.
E per tali impianti, mezzi, macchinari e attrezzature, i Responsabili delle attività di manutenzione interessati “gestiscono una specifica Scheda di Manutenzione nella quale vengono riportate tutte le informazioni utili per una corretta manutenzione, in particolare: tipologia dell’impianto, del mezzo, del macchinario o dell’attrezzatura; tipologia di intervento di manutenzione; frequenza di intervento”.
La Scheda di Manutenzione “definisce tutti gli interventi di manutenzione ordinaria o preventiva che il Personale aziendale interessato deve effettuare ad intervalli predeterminati. Tali interventi sono quelli che l'esperienza aziendale suggerisce, tenuto conto, laddove necessario, di quanto consigliato dal Libretto di Uso e Manuale di Manutenzione predisposti dal Costruttore”. Ed è cura del Rappresentante della Direzione - su segnalazione dei Responsabili delle attività di manutenzione interessati – “organizzare specifiche attività di addestramento finalizzate ad una più idonea utilizzazione dei mezzi, delle attrezzature e degli strumenti, con particolare attenzione agli aspetti relativi all’ambiente e alla salute e sicurezza sul lavoro”.
La seconda fase è invece relativa alla programmazione della manutenzione e registrazione delle attività di manutenzione.
Infatti una volta definiti gli interventi di manutenzione necessari, i Responsabili delle attività di manutenzione interessati “predispongono su base annuale il Programma Annuale di Manutenzione in cui definiscono gli interventi di manutenzione da eseguire per ogni impianto, mezzo, macchinario e attrezzatura, che sottopongono alla verifica e all'approvazione del Rappresentante della Direzione. Tale programma viene quindi divulgato a tutto il Personale incaricato delle attività di manutenzione”.
Si segnala che le attività di manutenzione “vengono effettuate dal Personale aziendale o, nel caso di ricorso a Organizzazione Esterna, dal Personale esterno nel rispetto degli obiettivi di salvaguardia ambientale e di tutela della salute e sicurezza nel luogo di lavoro”.
In particolare lo stato di utilizzabilità degli impianti, dei mezzi, dei macchinari e delle attrezzature “viene verificato di volta in volta dal Personale aziendale al momento della loro effettiva utilizzazione durante lo svolgimento delle attività operative ed al momento della conclusione delle attività stesse. In caso di guasto o malfunzionamento di un impianto, di un mezzo, di un macchinario e di un’attrezzatura, il Personale aziendale mette al corrente il Responsabile delle attività di manutenzione interessato affinché, con il Rappresentante della Direzione, siano stabilite le necessarie azioni per ripristinarne l'utilizzabilità e la funzionalità”.
Si sottolinea che “tutte le attività di manutenzione effettuate, siano esse ordinarie, straordinarie, preventive e/o correttive, vengono registrate a cura del Personale aziendale che le ha effettuate sulla Scheda di Manutenzione in corrispondenza del relativo spazio riferito alla particolare tipologia di intervento eseguito, con registrazione delle eventuali parti di ricambio sostituite e della data degli interventi effettuati. Qualora per un intervento di manutenzione si fosse ricorso ad una Organizzazione Esterna qualificata, è cura dei Responsabili delle attività di manutenzione interessati, con il supporto del Rappresentante della Direzione, verificare e registrare quanto eseguito, allegando alla Scheda di Manutenzione copia degli interventi effettuati comprovati dai Rapporti di Assistenza Tecnica e/o dalle Fatture emesse dall’Organizzazione Esterna”.
Infine la terza fase è relativa all’analisi degli Interventi di Manutenzione.
Infatti ogni anno – “prima di ripristinare per uno specifico impianto, mezzo, macchinario od attrezzatura la relativa Scheda di Manutenzione con gli interventi di manutenzione preventiva da eseguire oppure prima di decidere per le relative attività di manutenzione” - il “Rappresentante della Direzione e il Responsabile delle attività di manutenzione interessato, con il supporto delle Funzioni interessate, esaminano gli interventi effettuati nell'anno precedente, al fine di valutare la necessità di modificarli nel tipo, nelle modalità e nella frequenza”.
Tutte le succitate attività vengono gestite e controllate mediante l’utilizzo del software di gestione delle manutenzioni “TangoQRP”.
Per concludere veniamo all’efficacia, ai fattori di successo e ai vantaggi della buona pratica: riduzione dei tempi di fermo dei macchinari, riduzione del numero di near-misses e di infortuni sul lavoro, miglioramento del clima organizzativo, partecipazione del personale incaricato al piano di manutenzione preventiva, ...
Tiziano Menduto

I contenuti presenti sul sito PuntoSicuro non possono essere utilizzati al fine di addestrare sistemi di intelligenza artificiale.